Numerical Simulations of A Back Grinding Process For …
PPT_Feb16 - Free download as PDF File (.pdf), Text File (.txt) or view presentation slides online. The document summarizes a numerical simulation study of the back grinding process for silicon wafers. The objectives were to develop a simulation tool to help optimize the process for Micron Technologies and understand the effects of process parameters.
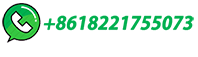