shibang/sbm nickel ore gravity concentration plant.md at …
shibang / sbm nickel ore gravity concentration plant.md. dushusbm c4a532c29b code. 19:24:26 +08:00
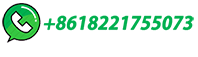
shibang / sbm nickel ore gravity concentration plant.md. dushusbm c4a532c29b code. 19:24:26 +08:00
Nickel processing - Extraction, Refining, Alloying: The extraction of nickel from ore follows much the same route as copper, and indeed, in a number of cases, similar processes and equipment are used. The major differences in equipment are the use of higher-temperature refractories and the increased cooling required to accommodate the higher operating …
Abstract Nickel is mostly extracted from sulfide ores, however, laterite ores account for over 60 pct of all nickel resources in the world, and despite its …
excellent cobalt-nickel separation primary leach liquor by Cyanex 272. However, manganese extraction from the leach liquor along with cobalt could not be avoided, thus increasing the cost of the process. For sulphide ores, there is another alternative; if the ore can be concentrated by flotation, matte smelting is used instead of leaching.
In the following article, Mr. John Wilson, Technical Services Asia, American P&I Club (Hong Kong Office), explains why nickel ore is considered as 'the world's most dangerous cargo'. Between 2010 and 2013, six vessels that loaded nickel ore in Indonesia sank during their voyages to China, resulting in the loss of life of 81 seafarers.
In limonitic ore, nickel replaces iron in the goethite crystal lattice, while in saprolitic ore, nickel and iron replace magnesium in various magnesium silicate …
♦ Flotation machine is a necessary equipment for nickel ore processing. It can effectively separate and purify materials according to their different properties. The outstanding advantages of flotation machine in production are: 1. The impeller of the equipment is always in motion, which can effectively remove the accumulated materials …
This paper describes a hydrometallurgical process for nickel recovery, by electrowinning, from purified sulphate heap liquors (Fig. 1) and presents the results and …
P204 (D2EHPA or HDEHP) This is used for first step to remove impurity for laterite nickel ore. DY319 high efficiency nickel cobalt co-extraction extractant for battery recycle, can take out nickel and cobalt together from Lithium battery electrolyte. DY272 Nickel cobalt separation extractant, it can take cobalt out from nickel cobalt solution ...
Nickel is an important strategic metal resource, which plays an important role in national defense, aerospace, new energy and other fields. In recent years, low-grade nickel sulfide ore (LGNSO) has become the main raw materials for nickel extraction due to the depletion of high-grade nickel sulfide ore resources [1].However, the effect of the …
This type of magnetic separation machine is used in wet separation processes for smaller than 1,2 mm ( – 200 mesh of 30-100 %) of fine grained red mine (hematite) limonite, manganese ore, ilmenite and some kinds of weakly magnetic minerals like quartz, feldspar, nepheline ore and kaolin in order to remove impurity iron and to purify them.
Flotation tests were performed on a skarn ore to attain the selective separation of scheelite (CaWO 4) from fluorite, apatite, and silicates. Fluorite and apatite constitute common gangue minerals in scheelite ores. Due to their similar surface properties and good floatability, the separation of scheelite from fluorite is particularly difficult.
The results of Figs. 3 and 4 agree with the before observations of Oshitani et al., who studied the dry separation of particulate iron ore in a gas-solid-fluidized bed [21]. They reported that ...
1. Introduction. The acid-leaching tailings of laterite nickel ore are a hazardous waste generated by the laterite nickel ore industry [1], [2], [3].As global demand for nickel continues to rise and nickel sulfide resources decrease, the extraction of nickel resources from laterite nickel ores the main development trend of the global nickel …
Nickel ores mainly include copper-nickel sulfide ore and nickel oxide ore (laterite nickel ore). The most important is the nickel ore flotation process, magnetic separation and gravity separation are usually auxiliary beneficiation methods.. We can customize nickel ore beneficiation process and equipment to achieve comprehensive utilization of …
Disclosed is a method for the homogeneous precipitation separation of iron and aluminum from a laterite nickel ore acid leaching solution, wherein the present invention belongs to the technical field of nonferrous metal wet metallurgy. The present invention comprises: finely grinding calcium carbonate or magnesium carbonate and mixing same with ...
nickel and iron oxide in nickel laterite ore, a C/O ratio of Table 1. Composition of nickel laterite ore (dry basis) and anthracite coal used in the current work (wt%).
DRY ASSAY. The dry assay of nickel (cobalt being at the same time determined) is based on the formation of a speise which will carry the cobalt, nickel, copper, and some of the iron of the ore in combination with arsenic. ... Solution and Separation. Two or three grams of a rich ore, or 5 to 10 grams if poor, are taken for the …
PDF | On Mar 11, 2019, Sait Kursunoglu and others published Hydrometallurgical Processing of Nickel Laterites—A Brief Overview On The Use of Solvent Extraction and Nickel/Cobalt Project For The ...
ABSTRACT Mineral and morphological characteristics of chromite ore strongly affect the separation efficiency while upgrading the low-grade deposits. Usually, chromite ore enrichment is carried out by using gravity separation due to high-concentration criterion between chromite and other minerals. However, chromite ore …
(1). Copper in copper-nickel sulfide ore mainly exists in the form of chalcopyrite, and nickel mainly exists in the form of free nickel sulfide such as fennelite and pentlandite. In addition, most of the nickel is mainly endowed in pyrrhotite in the form of similar phenomena, so the most important process of beneficiation of copper-nickel …
The magnetic separation efficiency of nickel from the laterite ore was evaluated using the recovery ratio of nickel R ni using the formula: (1) R Ni = m Ni × β Ni M Ni × γ Ni × 100 % where m Ni is the mass of the magnetic product, g; β Ni is the nickel content in the magnetic product, wt.%; M Ni is the mass of the reduction product, g ...
Dry slag need crushing grinding, water slag uses magnetic separation or gravity separation directly. Ushing Grinding And Flotation Nickel - baoli-forklifts.co.za Pilot scale test of producing nickel concentrate from lowgrade . using pelletizing, rotary kiln reduction and magnetic separation process on a .
High Field Intensity Nickel Magnetic Beneficiation Nickel Ore Beneficiation with High Intensity Permroll Units Nickel ore magnetic beneficitiation… Read More 19 June 2021 29 August 2021 Tagged beneficiation, magnetic separator, nickel, nickel beneficiation, permroll, roll magnetic separator
The characteristics of dry processing are simple process, no need for chemicals, and environmentally friendly. process flow. 1.Ore preparation:Crush the raw ore into smaller particles for the subsequent sorting process. 2.Dry crushing:The crushed ore is further crushed through a dry crusher to improve the particle size uniformity of the ore.
The dry-processed ore was placed on a sample stage of a computer-controlled contact angle measuring instrument (SL200C, China), and the contact angle was measured. ... Sodium phytate shows more efficient selectivity than conventional CMC and guar gum inhibitors in the flotation separation of copper-nickel sulfide from talc. …
In anticipation of future demands, a comprehensive understanding of the chemical and mineralogical characteristics of nickel-bearing minerals is a prerequisite to devising effective nickel …
Magnetic Separation as Part of New Nickel Concentrate Processing Technology at Kola MMC: Performance Analysis and Upgrade. Part I: DOI: 10.17580/tsm.2022.03.07: ... 15. Liu Zhuanqing. Dry-separation magnetic roller ore separation device. Patent CN212143048 (U). Applied: 2020.12.15. 16. Wang Yucheng, Cheng Baojun. Segmented dry magnetic ...
Flotation separation: Send the qualified copper-nickel ore into the mixing tank, stir thoroughly and then send it to the flotation machine.The unqualified ore particles after coarse crushing will ...
The separation of copper from nickel is based on the fact that there is an appreciable difference in the pH at which the two metals are extracted. Copper can be extracted, with very small amounts of nickel, at pH 6.0 to 6.5, while nickel is extracted from the copper raffinate at pH 8.0 to 8.2.
حقوق النشر © 2024.Artom كل الحقوق محفوظة.خريطة الموقع