Crushing Optimizing the Process
Optimization of a Final Crushing Stage This method applies to other crushers where a control variable is available The crushers are the last size reduction stage in the value …
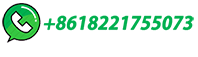
Optimization of a Final Crushing Stage This method applies to other crushers where a control variable is available The crushers are the last size reduction stage in the value …
improve the performance of a jaw crusher, is mainly determined by the kinematic features of the liner to optimize the frame, design the chamber and recognizing the crushing ... Optimization of Jaw Crusher G. Kirankumar J Advance Research and Innovations in Mechanical, Material Science, Industrial Engineering and Management - ICARMMIEM …
The current design of the movable jaw structure of the traditional jaw crusher is unreasonable with heavy weight. The parameterized entity modeling of the movable jaw is carried out by using Pro/Engineer Wildfire5.0 software. Through finite element analysis by using the ANSYS software, the response surface method (RSM) is utilized to optimize …
The present study investigates the effects of feeding properties on rock comminution by a laboratory scale jaw crusher. For this purpose, detailed crushability tests were carried out on four ...
To accurately predict fatigue life and reliability of the forage crusher rotor, the stress load spectrum of the rotor is obtained via the two-way fluid-structure coupling method, which calculates the coupled flow field in the forage crusher and rotor structure. ... After optimization, the fatigue life cycles of the rotor are increased from 1. ...
Optimization of Process Parameters for a Vertical Shaft Impact Crusher through the CFD-DEM Method Ke Sun (0009-0007-3953-9176), Limei Zhao (0009-0008-7307-0890), Qitao Long (0009-0002-3258-2175) ... Keywords: VSI crusher, working parameters, optimization, CFD-DEM Introduction VSI crusher is an increasingly used production …
The Optimization of Jaw Crusher with Complex Motion Aimed at Reducing Stroke Feature Value of Its Outlet 391 Rectangular coordinate system whose the origin base on the center of the crank rotation is built. The left direction in horizon is defined as increasing direction of Y axis and the ...
The optimization of cone crushers was studied while considering the output flow rate as an objective function and the flakiness and particle size models as …
Inspired by the bionic wear-resistant structure, the shape and parameters of an impact crusher chamber are optimized. Taking both crusher strength and crushing effect into consideration and using discrete element method, the parameters of the impact crusher chamber were properly optimized.
This research involves the optimization of aggregate production using the Taguchi approach to maximize the production rate of Gneiss stone. The L18 orthogonal …
crusher carefully. Optimization of a Final Crushing Stage . Optimization of one parameter (CSS) can be done by sampling and analysis The invested time and lost production will quickly be repaid by increased productivity Combine product yield and economic aspects
Current research on gyratory crushers has predominantly focused on structural optimization, comminution performance, and wear resistance. Chen et al., 2020, Chen et al., 2021a, Chen et al., 2021b) conducted a study employing the DEM to …
A dynamic performance prediction model of the gyratory crusher was established using the kriging interpolation method. Finally, based on the prediction model, the particle swarm optimization (PSO) algorithm was applied for the multi-objective optimization of the gyratory crusher.
Download Citation | Optimization of a New Knife Crusher to Increase Olive Oil Quality | Olive crushing has the purpose of breaking the olives, creating a paste made up of all the vegetable parts ...
The method developed for multi-criteria optimization of the crusher can be effectively used to optimize the parameters and structure of other types of crushing machines. Based on the results of the performed …
Therefore, both productivity optimization and product quality optimization are taken into account, the optimal performance parameters of the crusher C900 were obtained, the mantle bottom angle is in the range of 50° to 60°, the length of the parallel zone is in the range of 140 mm–190 mm, and the eccentric angle is in the range of 1.4°–2°.
Huang et al. (Huang et al., 2007) introduced a new crushing chamber geometry design of cone crusher based on the use of equations of motion and the population balance model (PBM), and it is used for crusher performance optimization.
Inspired by the bionic wear-resistant structure, the shape and parameters of an impact crusher chamber are optimized. Taking both crusher strength and crushing …
Keywords: Centrifugal crusher, energy cost, crushing circuit optimization Introduction In crushing circuits the feed material to the crusher is not broken below the desired size in one pass and for this reason the product is usually screened. The coarse fraction returns to the crusher through a system of conveyor belts.
The straw micro-crusher developed by this research group is capable of performing crushing and classifying operations simultaneously. Its structural composition is depicted in Fig. 1, comprising primarily two components: the crushing device and the classifying device.The crushing device comprises the crush cutters, crush chamber, feed …
Mathematical modeling and optimization of the design parameters of the working chamber and the executive body (roll) of a single-roll gyratory shaft crusher, designed for crushing strong rocks ...
Purpose: To extend the dephasing optimization through coherence order pathway selection (DOTCOPS) algorithm, originally designed solely for gradient crusher schemes, to include tailored phase cycling schemes for arbitrary pulse sequences and arbitrary number of coupled spins. Theory and methods: The effects all possible nested and …
In parallel to the works by Lindqvist on liner wear, Ma et al. (2016) emphasized the importance of an accurate cone crusher model for process optimization and proposed a heuristic model that correlates the material hardness, compression ratio, and particle size distribution with the liner pressure during crushing. Based on this …
This research involves the optimization of aggregate production using the Taguchi approach to maximize the production rate of Gneiss stone. The L18 orthogonal array has been used to investigate how the CSS, throw, eccentric speed, and particle size affect the products of the cone of the crusher (its cumulative weight fraction). The CSS, …
The guideline for the effective optimization of the crusher system is likely the instant linkage between filed data, the demand of PSD from the CFB, and the proper organization of the crusher system. The current study is to establish a Aspen Plus model to optimize the coal gangue crushing circuit in terms of the combustion performances of the ...
The gyratory crusher is one of the most important mineral processing assets in the comminution circuit, and its production performance directly impacts the circuit throughput. Due to its higher energy utilisation rate for rock breakage than semi-autogenous (SAG/AG) milling, it is a common practice in operations to promote and optimise primary …
DOI: 10.21062/mft.2024.028 Corpus ID: 268664034; Optimization of Process Parameters for a Vertical Shaft Impact Crusher through the CFD-DEM Method @article{Sun2024OptimizationOP, title={Optimization of Process Parameters for a Vertical Shaft Impact Crusher through the CFD-DEM Method}, author={Ke Sun and Limei Zhao …
Cone crushers are used in the mineral, mining, and aggregate industry for fragmentation and production of rock materials. Cone crusher control systems are widely used for machine protection, wear compensation and, to some extent, increasing production. These systems ordinarily focus on the crusher and not the yield of production process. In this …
Key design parameters (oscillating speed, closed size setting, base angle of cone, eccentric angle) which affect cone crusher performance were studied for the cone crusher performance optimization.
A prediction model of the crusher performance is obtained. Based on this, multi-objective optimization of the crusher performance is performed based on the genetic algorithm, productivity and power density is increased by 36% and 26%, respectively. The optimized crushing force is approximately twice the original one.
حقوق النشر © 2024.Artom كل الحقوق محفوظة.خريطة الموقع