Iron Ore Pellets Manufacturing Plant Project Report 2024
IMARC Group's report titled "Iron Ore Pellets Manufacturing Plant Project Report 2024: Industry Trends, Plant Setup, Machinery, Raw Materials, Investment Opportunities, Cost and Revenue ...
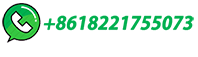
IMARC Group's report titled "Iron Ore Pellets Manufacturing Plant Project Report 2024: Industry Trends, Plant Setup, Machinery, Raw Materials, Investment Opportunities, Cost and Revenue ...
In this paper, we propose and assess a potential design for a fossil-free steelmaking process based on direct reduction of iron ore with hydrogen. We show that hydrogen direct reduction steelmaking needs 3.48 MWh of electricity per tonne of liquid steel, mainly for the electrolyser hydrogen production. ... To derive annual capital cost …
capital cost for processing iron ore Mobile Crushers all . capital cost for processing iron orePilot plant tests confirm Hawsons iron ore high grade low costpdf 15 Mar 2013 a product that should be among the best iron.
The direct reduced iron process consumes 1.5 tonnes of iron ore for each tonne of crude steel at a price of $144/tonne iron ore (Vogl et al., 2018). The process assumes conversion rates of 1.2 tonnes DRI per tonne of crude steel ( IEA, 2020b ) and 1.03 tonne crude steel per tonne of hot rolled steel ( Duarte, 2011 ).
Cost of New Iron Ore Mining Equipment. … iron ore cone crusher with high-efficiency has excellences for iron ore crushing, high productions and low upkeep. capital cost for processing iron ore | heavy industry
Operating cost including iron ore, coke, energy, labour, and services, is around 415 €/ton for a conventional steel mill, and the share of a reducing agent (coal) is around 84 €/ton (Mayer et ...
The Taconite Iron Ore Processing NESHAP (codified at 40 Code of Federal Regulations (CFR) part 63, subpart RRRRR) applies to each new or existing ore crushing and handling operation, ore dryer, pellet indurating furnace, and finished pellet handling operation at a taconite iron ore processing plant that is (or is part of) a major source of …
Mining of iron ore is a highly capital- and energy-intensive process. ... (LCA) of the mining and mineral processing of iron ore in Australia was carried out in this chapter using SimaPro LCA software as a case study. The environmental impacts ... For these studies, environmental, cost, and social data of relevant unit processes are collected ...
The strategic review also recommended a two-pronged action plan to improve the net present value of the project by reducing processing plant capital costs further and accessing higher grade ore ...
On 23 March 2023, BHP signed an agreement with global engineering firm Hatch to design an Electric Smelting Furnace (ESF) pilot plant with the aim of demonstrating a pathway to lower carbon dioxide (CO 2) emissions intensity in steel production using iron ore from our Western Australia Iron Ore (WAIO) mining …
Semantic Scholar extracted view of "MINERAL PROCESSING EQUIPMENT COSTS AND PRELIMINARY CAPITAL COST ESTIMATIONS" by E. Parkinson et al. ... As iron ore processing is … Expand. PDF. Save. Techno-Economic Analysis of Coal Preparation Plant Design Using Siu-Sim Simulator.
An initial capital cost of US$470 million to build the project (AACE - International Class 5 Estimate). ... The Project consists of a pelletizer at the Port Saguenay site to process iron ore concentrate into DR grade pellets in order to supply the growing global electric arc furnace steel production market. The process flow sheet includes the ...
Mining of iron ore is a highly capital- and energy-intensive process. Life cycle assessment (LCA) of the mining and mineral processing of iron ore in Australia …
capital intensity and operating costs," Ms Gaines said. "In developing the Iron Bridge Project, Fortescue has demonstrated and refined each step of the ore processing system and conducted full-scale trials. Our focus has been to create the most energy and cost-efficient ore processing facility, tailored to the specific ore we will mine. We are
An iron ore company is considering investing in a new processing facility. The company extracts ore from an open pit mine. During a year, 1,00,000 tonnes of ore is extracted. If the output from the extraction process is sold immediately upon removal of dirt, rocks and other impurities, a piece of Rs. 1,000 per tonne of ore can be obtained.
The capital cost for a typical 4.0 Mt per annum integrated steelmaking facility is in the order of US$4 billion. That compares to the relatively modest cost of relining a blast furnace, which we estimate are …
Iron ore pelletization is a critical aspect of the steel manufacturing process, providing a method to utilize fine iron ore particles and beneficiate lower grade ores, which enhances the overall output and efficiency of steel production processes. Pelletization involves converting iron ore fines into compact pellets, which are then used in blast …
The latest report titled "Iron Ore Production Cost Report" by Procurement Resource a global procurement research and consulting firm, provides an in-depth cost analysis of the production ...
Iron Ore Beneficiation & Processing Fundamentals is part of Informa Corporate Learning's Mining category collection – the leaders in training and knowledge. ... Compare the likely capital and operating costs of each upgrading process; Review the factors which might lead to a successful project;
The results show that the EU27 has the third highest production costs for hot rolled coil via the integrated route (458 EUR/t). The main contributors to these costs are the raw material costs 65%, the 'other costs' 27% and energy costs 17%. The CO 2 cost is included in 'other costs' and for the EU27 represents 2% of the total production ...
following stages of the extraction process Drill Blast Load Haul Prepare ground for blasting Break the ground Load broken ground into trucks Haul ore and waste Process Issues can add 10 to 25% to downstream costs through: • Damage to fleet, ore body, mine plan • Inefficient processing • Waste of explosive • Re-work
6.3.1.1 Cost Estimation for Preliminary Feasibility Studies Estimation of capital and operating costs of a proposed min ing venture is usually required after ore reserves …
Iron Ore Market Size & Trends "2030 iron ore market value to reach USD 301.86 billion" The global iron ore market size was estimated at USD 289.72 billion in 2023 and is expected to grow at a CAGR of 1.4% from 2024 to 2030. The consumption of iron ore worldwide is anticipated to be driven by the global demand for construction steel.
The estimated greenhouse gas emissions were 11.9 kg CO 2 e for mining and processing 1 tonne of iron ore. The embodied energy values were 153 MJ/t ore for iron ore. The results showed that loading and hauling made the largest contributions (approximately 50%) to the total greenhouse gas emissions from the mining and processing of iron ore.
The Tecnored process can use low-cost materials (e.g., low grade iron ore fines, low-cost fuels). Its smaller design means it requires less power and less pressure within the furnace. It achieves full metallization (up to 99 percent). The process takes just 0.5 h compared to a typical blast furnace process, which takes up to 8 h. However, this ...
The plant is expected to cost US$302 million and is approximately one-third of the total cost of the project, which is pegged at $902 million according to capital cost estimates released last year.
Rio Tinto's IOC has secured C$18.1m ($13.3m) from the Canadian Government to advance the decarbonisation of iron ore processing at its Labrador West operations.. The investment, allocated from the Low Carbon Economy Fund, is set to reduce IOC's reliance on heavy fuel oil during the production of iron ore pellets and …
Capital Expenditure by project category (nominal to 2020 and real thereafter) ... Q2 2024 iron ore value-in-use adjusted costs are up 3.5% compared to …
simplifies the process design. In addition, as the processing will be sequenced it allows for a common crushing and grinding circuit followed by separate process plants to treat each ore type. 2. PROCESS DESCRIPTION The processing plant will be designed with two distinct operating mode. The mode used s will depend on the ore being treated.
Iron ore 2 is the key input in pig iron production, which is then used to manufacture steel. Iron ore as well as many other commodities is noted for both persistent trends and rapid turnarounds in terms of global prices. There was a long period of declining prices in real USD terms from mid-1960s to early 2000s, which led to underinvestment in …
حقوق النشر © 2024.Artom كل الحقوق محفوظة.خريطة الموقع