The ball to powder ratio (BPR) dependent morphology and …
The powder refinement process and the influence of ball to powder ratio (BPR) on the morphology and microstructure of tungsten powder were investigated. ...
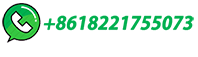
The powder refinement process and the influence of ball to powder ratio (BPR) on the morphology and microstructure of tungsten powder were investigated. ...
The ignition time (t ig) of the mechanically induced self-sustaining reaction (MSR) process involving the formation of TiB 2 from Ti/2B elemental mixtures was used to study the influence of the ratio (k = -ω v /ω d) between the rotational speed of the supporting disc (ω d) and vials (ω v) on the milling efficiency of a Pulverisette 4 …
This literature review explores the effects of changes in ball mill jar size, ball-to-powder ratio, and process control agents (PCA) on mechanical attributes. 2.3.1. Impact of Different Ball Mill Jars on …
Highly transparent LaGdZr 2 O 7 ceramics were fabricated by solid reactive sintering using the ball-milling mixed raw powder, and the transparency of samples can be significantly enhanced by optimizing the ball-to-powder weight ratio. The ratio effects on the evolution of morphology and particle size distribution of mixed powder, as well as …
Aluminum powder of 99.8% purity (MFCD00134029) was provided by Alfa Aeasar Company. Stearic acid (97% purity, Fisher Scientific-AC17449-0010) was used as the process control agent (PCA) and 3 wt% of it was mixed with the aluminum powder prior to milling.High energy ball milling was done in a planetary ball mill (Torrey Hills-ND2L) …
The effects of high energy milling on the shape, size and low temperature sinterability of plate-like alumina powder was studied. The milling effects were studied under three different processing conditions, designed by varying the charge ratio and the milling medium. 10:1 and 20:1 ball to powder charge ratios were considered in wet and …
The initial powders were ground via a high-energy planetary ball mill with a ball-to-powder weight ratio of 3:1 for 1 h. The rotating speed was kept at 200 rpm. The stainless steel vial with the capacity of 1 L and the stainless steel balls (10 mm in diameter) were matched with the planetary ball mill.
Under the milling speed of 600 r/min, ball to powder ratio (BPR) of 10:1, and milling time of 4 h, the grain size, lattice strain, and average particle diameter of the composite powder were measured to be 48.4 nm, 0.247 %, and 21.04 μm, respectively, with the particle morphology being nearly spherical.
Size-reduced turning chips (30 g) by cutting process were milled in the planetary ball mill with a ball to powder weight ratio of 3:1 and ethanol (30 mL) using 250 rpm rotation speed. Prior to the fabrication of final Cp-Ti metallic powders, a wet milling process was used to obtain more homogeneous initial particle size. ...
A mechanical classifier often receives its feed from a ball mill and produces (1) finished material which overflows to the next operation and (2) sand which returns to the mill for further size …
Mill speed, ball to powder ratio (BPR), geometry of milling jar, milling time, process controlling agent (PCA), milling environment etc. are the major variables that influence the nature of the milled product [15–19] and hence these parameters should be optimized to obtain the desired phase and grain size of the material. In the present study ...
The maximum power draw in ball mill is when ball bed is 35-40 % by volume in whole empty mill volume. Considering that ball bed has a porosity of 40 %, the actual ball volume is considered to be ...
The milling process is carried out in a high-energy ball mill, which generates a high impact force on the powders, leading to deformation, fracturing, and cold welding of the particles ...
The small ball diameter had a significant effect on the particle morphology because of the repetitive ball–powder–ball collisions. Download: Download high-res image (482KB) Download: Download full-size image; Fig. 9. Aspect ratio of copper powder ball milled at various rotation speeds for (a) 1 mm and (b) 10 mm ball diameters.
Wet milling is considered more effective than salt assisted milling and dry milling (Peterson et al. 2012). Increase in a ball to powder ratio decreases the particle size (Zakeri et al. 2012) but ...
High energy ball milling (HEBM) is known as an economic, simple and yet powerful method for the production of nanostructured and amorphous materials [1].The prolonged milling of powder mixtures, results in the formation of supersaturated solid solution, non-equilibrium intermetallic compounds as well as the formation of silicides, …
Abhinay Sreeram. Measure the quantity of solvent (water/non aqueous based) that can be filled in your grinding jar (fill it upto the neck). Suppose after weighing the solvent you get 100 gm ...
Increment on the ball to powder ratio (BPR) reduces the mechanosynthesis time of Re 2 C.. Mechanosynthesis of Re 2 C was obtained at BFR of 230:1, 30 min of milling, accumulated energy > 500 k J g and transferred energy > 2.656×10-14 kJ.. Cold working and defects generated during high-energy ball-milling do …
The elemental powders were mixed in equiatomic composition and milled in a planetary ball mill (PBM-04, Canada) in an inert (Argon) environment to avoid oxidation. ... Other variables such as PCA type, ball-to-powder ratio, and mass ratio of the milling balls were kept fixed as used in Section 3.1. Two output responses, particle size and grain ...
This literature review explores the effects of changes in ball mill jar size, ball-to-powder ratio, and process control agents (PCA) on mechanical attributes. 2.3.1. Impact of Different Ball Mill Jars on Mechanical Properties . Ball milling is a widely used technique for the preparation and modification of various materials. The capabilities of ...
Therefore, the ball milling treatment was used to remove sharp corners and smooth the surface of the precursor powder particles. Ball milling process was conducted in a planetary ball milling machine (QM-3SP04, Nanjing University Instrument Factory) equipped with four nylon ball mill tanks with an internal volume of 50 mL.
Under the milling speed of 600 r/min, ball to powder ratio (BPR) of 10:1, and milling time of 4 h, the grain size, lattice strain, and average particle diameter of the …
This process utilizes ball mills to weld and fuse powder particles through a combination of impact and plastic deformation. In the late 1960s, this method was employed to produce nickel-iron alloys. ... If the ball-to-powder ratio is too high, the balls cannot move efficiently anymore, reducing the efficiency of the alloying process. To ...
Nanostructured SAF-2507 super duplex stainless steel powders were prepared in a Retsch PM-100 planetary ball mill for 20 h at 5:1 and 10:1 ball to powder …
The effects of the ball-to-powder diameter ratio (BPDR) and the shape of the powder particles on EDEM simulation results and time in the planetary ball mill was investigated. BPDR was varied from 1 to 40/3 by changing the powder particle diameter from 8 to 0.6 mm. ... A planetary ball mill is used for ultrafine grinding and can be used …
The effect of ball size on the particle size reduction has been investigated first for varying rotation speed of the container. Percent passing and size distributions of the milled Al 2 O 3 powder are shown in Fig. 1, Fig. 2, respectively, as a function of particle size for varying ball size.The average particle sizes (d 50) of the milled Al 2 O 3 powder …
A planetary type ball mill is economical, simple to operate, and ideally suited for small-quantity batch type synthesis of powders and alloys and for reactive processing of powders. The size of the jar and balls, rotational speed, milling duration, ball-to-powder ratio, jar material, milled material, and temperature are the most important ...
Ball to Powder Ratio - Free download as PDF File (.pdf), Text File (.txt) or read online for free. good
So i'll have to increase the ball to powder ratio in a low energy ball mill i.e fill the jar with 40% balls and some 20% ethanol. Btw i was initially gonna dry mill the carbide powders.
Milling speed, grinding time, and ball-to-powder ratio affect the particle size obtained and morphology of the solid particles [5]. 3.2. Tumbler ball-mill. Tumbler ball mill utilizes gravitational force to exert force on the solid particles. The milling balls rotate axially due to friction against the wall, and it rolls down and impacts against ...
حقوق النشر © 2024.Artom كل الحقوق محفوظة.خريطة الموقع