Steel Production
The blast furnace is the first step in producing steel from iron oxides. The first blast furnaces appeared in the 14th century and produced one ton per day. ... The blast furnace uses coke, iron ore and limestone to produce …
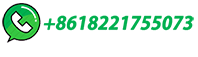
The blast furnace is the first step in producing steel from iron oxides. The first blast furnaces appeared in the 14th century and produced one ton per day. ... The blast furnace uses coke, iron ore and limestone to produce …
"Steel is everywhere. It builds our cities, our homes, our cars, everything. But the process of making steel from iron ore takes a lot of energy, it accounts for about 8% of global CO 2 emissions. So, for over 10 years …
The coke is mixed with iron ore and limestone to make molten iron, which is then further treated and heated to make steel. Generalized diagram showing how steel is made. In the steel-making process, coke is used in the blast furnace as a (1) fuel to produce added heat; (2) chemical-reducing agent for the reduction of iron oxides; and …
Steel making is a sophisticated process that turns iron ore into steel, involving methods like the Blast Furnace and Electric Arc Furnace to produce various grades of steel. The industry emphasizes sustainability by using additives and recycled materials while ensuring quality through rigorous testing for diverse applications.
Then, the ore is combined with coal or coke, which removes the impurities and other minerals, making the elementary Iron ready for steel production. However, lately, recycled steel has been used more, contributing to sustainable practices by reducing the need for raw materials and energy. The Blast Furnace Process Explained. In the blast ...
This results in Pig Iron which is then further used as raw material in Electric Arc Furnace to make steel. About 1.5 tons of iron ore is needed to produce 1 ton of steel. Electric Arc Furnace if only for melting of steel, later it goes for secondary refining and degassing where all the refinement is done and gases are brought within acceptable ...
The advantage of steel over iron is greatly improved strength. The open-hearth furnace is one way to create steel from pig iron. The pig iron, limestone and iron ore go into an open-hearth furnace. It is heated to …
The most common way it's produced involves mining iron ore, reducing it in a blast furnace through the addition of coal, and then using an oxygen furnace to burn off excess carbon and other impurities. ... During that work, he began to conceptualize a similar electrochemical process to make iron, the precursor to steel. But it wasn't until ...
Homepage /; About Making steel. Steel is made from iron ore, a compound of iron, oxygen and other minerals that occurs in nature. The raw materials for steelmaking are mined and then transformed into steel using two different processes: the blast furnace/basic oxygen furnace route, and the electric arc furnace route.
The Basic Oxygen Steelmaking (BOS) process is one of the most widely used methods for transforming pig iron into steel. This process, developed in the mid-20th century, is highly efficient and capable of producing large quantities of steel in a short time. In the BOS process, molten pig iron is poured into a large vessel called a converter.
Steel making is a sophisticated process that turns iron ore into steel, involving methods like the Blast Furnace and Electric Arc Furnace to produce various grades of steel. The industry emphasizes …
The Bessemer Process for Steel production and; The Open Hearth Process of Steelmaking; Steel manufacturing Principle of the Bessemer Process. The main raw materials for Steel production in a blast furnace …
The steel-making process is an elaborate one, involving numerous steps, each playing a crucial part in reaching the final product. Let's delve into these steps for a detailed understanding: Iron Making: This is the first step of the steel-making process, where iron ore, mixed with coke and limestone, is heated in a blast furnace. The heat ...
Ironmaking 101 – From Ore to Iron with Smelting and Direct Iron Reduction. Figure 1: Steelmaking byproducts for blast furnace (BF), basic oxygen furnace (BOF) and electric arc furnace (EAF) processes. …
The sintering process is an intricate system with a protracted process flow. The steps in the manufacturing line are primarily composed of the ingredients and mixing process, the sintering operation process, and the treatment of the sintered ore [39, 40].2.2 Important parameters and characteristics of sintering process. As shown in Fig. 2, all …
Helios claims that replacing carbon with sodium to prise oxygen out of iron ores -- an early stage in steel manufacturing -- can slash carbon emissions, energy and production costs
Making steel. At Scunthorpe, we use the Basic Oxygen Steelmaking (BOS) process – our modern convertors (or vessels) take a combined charge of scrap and liquid iron of up to 330 tonnes and convert this into steel in just 25 minutes. When the liquid iron arrives at the BOS Plant, it's poured from the torpedoes into refractory-lined charging ...
Coke is used as a fuel and a reducing agent in melting iron ore. It is produced by baking coal until it becomes carbon by burning off impurities without burning up the coal itself. When coke is consumed it generates intense heat but little smoke, making it ideal for smelting iron and steel. Prior to the 1880's, steel was produced using charcoal.
Before iron ore can be used, oxygen must be removed from it. Known as 'reducing', this can be done either in the blast furnace, where hot air is injected into a continuous feed of coke, sinter and lime, or by the direct reduced iron (DRI) process. The result from both is liquid iron, which is then transported to the basic oxygen furnace. The blast furnace …
The Steel Manufacturing Process. The steel production process is a multi-faceted journey that begins with extracting and processing iron ore, a primary raw material essential to steel making. …
Iron processing - Smelting, Refining, Alloying: The primary objective of iron making is to release iron from chemical combination with oxygen, and, since the blast furnace is much the most efficient process, it receives the most attention here. Alternative methods known as direct reduction are used in over a score of countries, but less than 5 percent of iron …
The third option for pig iron is to push the refining process even further and create steel, which we'll examine on the next page. Iron Advantage Between the 15th and 20th centuries, some countries had an industrial leg up on the competition due to the availability of iron ore deposits.
How steel is made. First, the raw materials, either iron ore or scrap iron (depending on the process), are converted into molten steel. The ore-based process uses a blast furnace or smelter and the scrap-based process uses an electric arc furnace. Next, the molten steel is poured and solidified in a continuous caster.
The Iron Ore, Coke and Limes ... Presentation will help to provide basic principle and brief overview of iron making to steel making process. which is cover each and every stage of iron and steel ...
The Sintering Process of Iron Ore Fines. Sintering plants are normally associated with the production of hot metal in blast furnaces in integrated steel pants. The process of sintering is basically a pre …
In the Blast Furnaces, we melt iron ore into liquid iron at high temperatures. Iron ore has a sand-like structure that can put out the fire in the furnace. Because of that, you can't put it in the furnace just like that. The ore is first baked to make it into porous chunks, or sinters. This is done in the Sintering Plant.
Making steel. Steel is made from iron ore, a compound of iron, oxygen and other minerals that occurs in nature. The raw materials for steelmaking are mined and then transformed into steel using two different …
WEB1. Raw Material Extraction. The steel-making process begins with gathering the essential raw materials: iron ore, coal, and limestone. Iron Ore: This is …
Figure 1: Steelmaking byproducts for blast furnace (BF), basic oxygen furnace (BOF) and electric arc furnace (EAF) processes. Source: World Steel Association (worldsteel) The first step in the production of steel or cast iron alloys is the reduction of iron ore—which contains iron oxide and gangue or mineral impurities—to unrefined, …
World resources are estimated to be greater than 800 billion tons of crude ore containing more than 230 billion tons of iron. The only source of primary iron is iron ore, but before all that iron ore can be …
حقوق النشر © 2024.Artom كل الحقوق محفوظة.خريطة الموقع