Jaw Crusher Explained
A crusher is a machine designed to reduce the size of large rocks to smaller rocks, gravel, sand, or rock dust; this is essential for efficient transport of the product via conveyors etc. Crushing is the first of many …
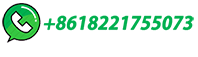
A crusher is a machine designed to reduce the size of large rocks to smaller rocks, gravel, sand, or rock dust; this is essential for efficient transport of the product via conveyors etc. Crushing is the first of many …
impact crusher impact crusher Both impact crushers and jaw crushers are used to reduce the size of materials, but they operate in different ways and are used for different applications. An impact ...
Impact crushers (impactors) reduce mineral materials such as concrete, asphalt, and rock in size producing a cuboid product. Learn how impact crushers work. ... or in a secondary crushing application (e.g. after a …
The Zoneding Mobile Jaw Crusher is a robust and efficient machine designed for various materials and applications. Here are some key specifications: Applied Materials: River pebbles, granite, basalt, …
How To Install And Use Jaw Crusher Properly? A jaw crusher is mainly composed of a frame, fixed jaw plate, movable jaw plate, side guard plate, adjusting seat, toggle plate, etc. As we can see from the jaw crusher diagram below, the structure of the jaw stone crusher is complex. Therefore, users must read the installation instructions and ...
If your application permits to use an impact crusher over a jaw and cone crusher setup there are numerous reasons that support the use of an impact crusher. Less fuel burn: Only one machine burns fuel. For …
Typically we're looking at the wear parts or the actual parts of the crusher that are impacted by the material. So if it's an impact crusher it would be the blow bars. If it's a jaw crusher it's the jaw dies or jaw plates. And most of the crushers that are out in the market you can flip the parts and double the life out of them.
How do jaw crushers work? Jaw crushers use compressive force to break down large materials into smaller, more manageable pieces. It has two crushing jaws (one is stationary while the other one is moving) that …
Another advantage of using an impact crusher is that it has a relatively low operating cost. The machine uses less energy than other crushers, such as jaw or cone crushers, and its impact force is …
To run an impact jaw crusher, follow these steps: Make sure the crusher is properly assembled and all safety guards and devices are in place and functioning properly. Start the crusher by turning ...
Application: Jaw rock crushers are mainly used to break large and hard materials into more manageable pieces, so people often use them as primary crushing, and if you have high requirements for crushing materials, you need to prepare secondary or tertiary crushing. Features: It has a large crushing capacity, and high efficiency, and is not easy to grind.
When comparing impact crushers, cone crushers, and jaw crushers, it's essential to understand their distinct functionalities to determine the right equipment for your specific application. As mentioned, an Impact Crusher is excellent for processing materials like asphalt and concrete into smaller, uniform pieces, thanks to their high-speed ...
The primary difference between an impact, cone, and jaw crusher is the type of crushing force they use. An impact crusher uses dynamic force to break down materials, whereas a cone crusher uses a ...
In general, the jaw is considered a more rugged and durable crusher. Jaw crushers are often used when material is very hard, such as granite. Jaw crushers operate at low speeds and tend to require less horsepower to operate. Jaw crushers have replaceable wear plates. Jaw crushers can be adjusted to produce a variety of …
To use an impact crusher, you will need to select the appropriate size and model for your specific needs. Some general steps for operating an impact crusher are: Pre-operational inspection: Before ...
The impact crusher and jaw crusher are two popular machines, each known for its specific strengths and uses. What sets them apart is how they crush materials, the type of stuff they handle, and the size of the products they produce. This piece dives into what makes impact crushers and jaw crushers different, looking closely at their ...
Jaw Crushers vs Impact Crushers. Impact crushers and jaw crushers are two of the most commonly used types. They both use compression to break down materials, but they use different …
If the jaw crusher is not properly maintained and repaired, the toggle plates may not be able to function properly, which can cause the crusher to fail prematurely. The solution to this problem is to follow the manufacturer's recommendations for the maintenance and repair of the jaw crusher, and to use high-quality, durable parts when …
On installation: installation of components of jaw crusher. Next, we will learn about the installation of jaw crusher from the parts of the frame, eccentric shaft and bearings, rod bolts, brackets, movable jaw plate, and dental plates. 1.The installation of the frame. The jaw crusher is installed on the concrete foundation.
Depending on your project you may want to combine the use of a jaw crusher and an impact crusher. A jaw crusher is a primary crusher that can reduce …
Check Impact Crusher. Before opening the crusher box, activate the RM Release System manually to loosen packed dirt and ensure the impact wall swings freely. Check for wear and damage and replace worn parts if needed.; If applicable, change hammers when you process large amounts of another material. Before closing, clean the edges of the …
Therefore, if you need your finished products to be much smaller in size and perfect in shape, use the cone crusher. Cone crusher VS Jaw crusher: Key differences Cone crushers and jaw crushers both perform well in quarries, aggregates plants, sand making plants, cement plants, etc. However, many still do not know which one to choose.
The exact crushers you need—jaw, cone, impact or gyratory—depend on the jobsite, the product you're making, and how much you need to produce. ... Jaw crushers have been around for nearly 200 ...
Impact crushers involve the use of impact rather than pressure to crush material. The material is contained within a cage, with openings on the bottom, end, or side of the desired size to allow ...
They are designed to protect the jaw crusher from the impact of heavy stones or other large objects that are being crushed into smaller pieces. Toggle plates are also used to adjust the size of the discharge opening …
Since they depend on high velocities for crushing, wear is greater than for jaw or gyratory crushers. Hence impact crushers are not recommended for use on ores containing over 15% silica ( et al., 1976). However, they are a good choice for primary crushing when high reduction ratios are required (the ratio can be as high as 40:1) and the ...
5. discharge fineness. Jaw crusher, as coarse crushing equipment, has larger discharge fineness, usually below 300-350mm (depending on the model). Impact crusher, as medium or fine crushing equipment, …
The reason jaw crushers have a higher percentage of fines and elongated particles is because of how they crush the material. Jaw crushers mainly use compression and impact forces to break things …
حقوق النشر © 2024.Artom كل الحقوق محفوظة.خريطة الموقع