what function does raw meal silo perform in cement manufacturing process
Process for non Process1 - SlideShare, Lump formation in cement silo ... aluminaand iron oxide are used in cement manufacturing process ... so in cement theL/D proportion is 3.in raw meal ... Go to Product Center. working principle of raw mill kiln plant – Grinding Mill China, » manufacturing process of plaster of ... Raw meal homogenizing ...
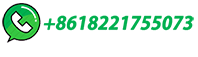