The Gravity Method in Iron Ore Exploration
The gravity method was first applied to iron ore exploration as a tool for detecting nonmagnetic ores, but advantages of this method over other exploration methods have also made it useful under certain geological conditions in the study of magnetic ores and regional structures favorable for the occurrence of iron ore. However, the gravity ...
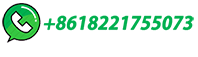