Reagents in iron ores flotation
Abstract. The role of reagents utilised in iron ores flotation is reviewed. Desliming and flotation stages should be performed at pH levels as low as possible to …
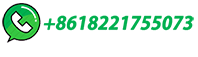
Abstract. The role of reagents utilised in iron ores flotation is reviewed. Desliming and flotation stages should be performed at pH levels as low as possible to …
Learn about the key stages in iron ore processing, including crushing, screening, and beneficiation techniques for optimal resource utilization. +86 ; xlyin@xinhaimining; ... c. Flotation: Flotation is a selective separation process that relies on the differences in the surface properties of the ore minerals. Chemical reagents ...
After carrying out a froth flotation separation, the products are as shown in Table 1. Using this data, calculate: (a) Ratio of concentration (b) % Metal Recovery (c) % Metal Loss (d) % Weight Recovery, or % Yield (e) Enrichment Ratio Table 1: Grade/recovery performance of a hypothetical copper ore flotation process.
This technique has a high utilization rate of RE resources and has been applied to industrial-scale production of ores from Bayan Obo, Mountain Pass and Weishan Lake with the process flow charts in Fig. 4. 55, 61 It is worth mentioning that the flotation feed of Mountain Pass and Weishan Lake is the raw ore, while the flotation feed of …
The flotation has been successfully applied to process the iron ore for the particle size (Ps) from 10 µm up to 150 µm. The presence of the slimes (Ps < 10 µm) is harmful on the reverse ...
In both cases, the flotation process adopted is a reverse cationic process with a preliminary desliming stage of flotation feed to remove materials with particle …
Overview of the Groveland Mine iron ore beneficiation process, utilizing direct flotation in acidic conditions (based on Houot 1983). Overview of the iron ore beneficiation process in the Qidashan ...
ABSTRACT. Recently, beneficiation of iron from low-grade ores with high impurities has been a matter of discussion. Flotation is one of the most effective technologies for the upgrading of low-grade, finely grained iron ores.
This work describes the concentration of iron ore slimes on a pilot scale by using a 500-mm diameter flotation column and a novel collector, which renders the use of a depressant unnecessary. The pilot …
Flotation is the most effective solution, both technologically and economically, when upgrading iron concentrates. Research regarding iron ore flotation began in 1931, demonstrating that reverse ...
Mineral Processing and Extractive Metallurgy Review An International Journal Volume 43, 2022 - Issue 1. Submit an article ... Starch is widely used as the depressant in iron ore flotation. The present paper attempts to highlight different facets of starch as an iron ore depressant. It reviews the important research papers that discuss …
In the recent past, iron ore resources from Brazil consisted of relatively high-grade iron ore, commonly processed via multi-stage crushing/screening, gravimetric concentration, magnetic separation, and reverse flotation. However, the high-grade iron ore reserves are in decline, resulting in the need to process the lower grade itabirite …
It should be added that segregation of laterite ores prior the flotation process has shown some improvement in upgrading nickel. The segregation process relies on the addition of calcium chloride or sodium chloride and carbon allowing the formation of nickel and iron chlorides at temperatures between 900 and 1150 °C. …
The significant applications of iron ore flotation are reviewed along with an abbreviated discussion on theory and reagent use. Problems or conditions which have …
In this paper, several studies describing the processing of iron ores via direct and reverse cationic and anionic flotation are reviewed. The objective of this review …
In Sivas-Divriǧi Iron Ore Concentrator 600,000 tons of tailings is discarded annually. There are already one million tons of tailings deposited in the ponds from the previous production activities.
In the recent past, iron ore resources from Brazil consisted of relatively high-grade iron ore, commonly processed via multi-stage crushing/screening, gravimetric …
The common processes used to remove sulfur from iron ore concentrates are flotation and roasting. At the same time, the latter is costly and produces environmental pollution, so the main direction of …
In India, China and Brazil, iron ore flotation is a commonly practiced separation technique with process control regarded as an integral part of flotation process operations. Mintek in South Africa developed an advanced flotation stabilization and optimization system, which was installed in Brazil's Vale's Cauè iron-ore-processing …
Special Issue Information. Dear Colleagues, Iron ore flotation is a key technique to concentrate intermediate-low-grade ore, in order to reach the market requirements for higher-grade concentrates of …
The Brucutu iron ore mine (Minas Gerais, Brazil) is Vale's largest iron producing operation achieving around 21 million tons per annum. Evaluation of flotation performance is of high importance as …
The flotation process is widely used in the mining industry to separate valuable minerals from ore, and the process relies on using specific types of ore. Usually used to concentrate various sulfide minerals, phosphates, and oxide minerals also need to be concentrated by flotation machines.For example, gold ore, silver ore, copper ore, …
The market requirements for higher-grade concentrates of iron to improve the productivity of the iron and steel industry, has increased the importance of the flotation process with respect to the conventional preconcentration …
This investigation addresses the interactive effect of process parameters on the processing of Indian iron ore slimes by using column flotation. The iron ore slime containing 58.7% Fe, 5.2% SiO 2 and 4.9% Al 2 O 3 was used for this investigation. The subsequent size analysis, chemical characterisation, desliming and column flotation …
The contamination of sulfur emanating from pyrrhotite in magnetite concentrates has been a problem in iron ore processing. This study utilized froth flotation to float pyrrhotite away from magnetite using collectors of xanthate and dixanthogen. It was found that xanthate or dixanthogen alone could not achieve selective separation between pyrrhotite and …
Iron ore flotation is generally concerned with the separation of the iron oxide minerals from those containing silica. For these ores the flotation method employed may be that which recovers iron minerals in the froth (direct flotation), or alternatively, that by which the siliceous gangue is contained in the froth product (reverse flotation ...
Generally, the particle size below 150 μm is discarded as waste (slimes) during the iron ore processing stage and stored in tailing dams. With the unprecedented demand for iron ore, the industries accumulated a huge amount of fines/slimes in tailing dams. ... Studies on the beneficiation of Indian iron ore slimes using the flotation …
The other is to reduce the sulfur content via the iron ore beneficiation process. As a sorting process, flotation plays a fundamental role in this. The objective of the test campaign described below was to reduce the sulfur content in an iron ore concentrate from 1.3 % to less than 0.4 %.
Reverse flotation of iron ore is now drawing more attention in iron ore industry as an efficient beneficiation process (Ma et al., 2011, Filippov et al., 2010, Araujo et al., 2005, Houot, 1983). In reverse cationic flotation, silica and silicates are floated after depressing the iron oxide by suitable reagents such as starch, dextrin, and CMC.
In India, China and Brazil, iron ore flotation is a commonly practiced separation technique with process control regarded as an integral part of flotation …
حقوق النشر © 2024.Artom كل الحقوق محفوظة.خريطة الموقع