Exploring the Efficiency of Magnetic Separation and Gravity
The presented work offers an innovative process scheme for valorizing Pb-Zn slag, which involves crushing, grinding, and separation techniques to concentrate valuable components (non-ferrous metals). ... Gravity concentration ( 13 shaking table) and magnetic separation (Davis separator and disk separator) were used to obtain the final ...
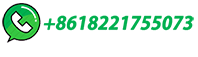