Iron ore concentrate vs fines: An In-Depth Comparison
Iron Ore Fines Market. 1. Lower Cost: Iron ore fines are generally cheaper than concentrates due to their lower iron content and higher impurity levels. 2. Demand for …
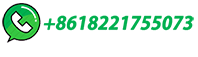
Iron Ore Fines Market. 1. Lower Cost: Iron ore fines are generally cheaper than concentrates due to their lower iron content and higher impurity levels. 2. Demand for …
The reduction of iron ore fines using fluidized bed has attracted more attentions in recent years since it has more advantages in energy consumption and environment protection over the conventional process. To better understand the reduction behavior of iron ore fines in a circulating fluidized bed (CFB), a mathematical model based on unreacted shrinking …
There are several processes for direct reduction of iron ore, principally gas-based shaft furnaces (Midrex and ENERGIRON processes) accounting for 76% and coal based rotary kiln furnaces (mainly in India) accounting for 24% of 2019 production (108.1 million ... Metallised DRI Fines Off-gas ines Iron Oxide Fines 2. Screening of individual ...
Carbon is used in the hematite ore pellet as a partial heat source for induration. Apart from this, it has several other roles in the pellet. To achieve the maximum benefit of carbon in pellet ...
This review focuses on the usability of iron ore ultra-fines for hydrogen-based direct reduction. Such technology is driven by the need to lower CO 2 emissions and energy consumption for the iron and steel industry. In addition, low operational and capital expenditures and a high oxide yield because of the direct use of ultra-fines can be …
Mandatory application of the iron ore fines schedule as per the IMSBC Code requirements: applies only to iron ore cargoes containing BOTH: (a) 10% or more of fine particles less than 1 mm (D 10 ≤ 1 mm) ; and (b) 50% or more of particles less than 10 mm ( D 50 ≤ 10 mm). However, if the total goethite content is 35% or more by mass, iron ore fines may …
This mathematical evaluation focuses on iron ore ultra-fines for their use in a novel hydrogen-based fluidized bed direct reduction process. The benefits of such a process include reduced CO2 emissions and energy consumption per ton of product, lower operational and capital expenditure, and a higher oxide yield. Typical samples of iron …
New Delhi: To increase the usage of available raw materials, the Ministry of Steel has directed integrated steel players to make use of iron ore fines in steel making after its beneficiation.As per sources, the ministry has also suggested that players look at options like acquiring coking coal mines abroad. This is aimed at increasing the …
The peak concentration of nitrogen oxides in the flue gas produced by the high-temperature roasting of the iron ore fines was only 30 ppm, indicating that the iron ore fines contained small ...
The peak concentration of nitrogen oxides in the flue gas produced by the high-temperature roasting of the iron ore fines was only 30 ppm, indicating that the iron ore fines …
The potential technology may be promoted through pilot trials in India. Keywords : Iron ore fines use, Sintering, Pellet making, Fluxed pellet, Hollow pellet, CPR pellet, Fluxed DRI, DRI granules, Iron cake, Iron …
Off-gas Fines 55 - 75 1 - 40 0.5 - 2.5 4.0 - 12.5 4 - 20 Iron Oxide Fines 62 - 68 0 0 2 - 5 2 - 5 Gangue = SiO 2 + Al 2O 3 + CaO + MgO . The preparation of D irect Reduced Iron Fines is as follows: 1. Collection of individual components . Metallised DRI Fines Off-gas …
a method of agglomerating iron ore fines comprising mixing fines with hot gases and thereby heating them to a temperature of about 450 to 650 F., moistening the gases and fines with an atomized spray of relatively cool water which does not immediately vaporize, thereby producing a water content of about 15 to 20 percent by weight in the gas …
testing of cargoes of iron ore fines so as to ensure that it is carried out in accordance with the IMSBC Code (the Code), which became mandatory worldwide on 1 January 2011. The relevant sections of the Code are Sections 4, 7 and 8. Provision of information The shipper must provide the master or his representatives appropriate
As the iron ore grade declines, the rate of increase in GHG emissions from mining accelerates. For example, when iron ore grade decreases from 40% to 35%, the average GHG emissions for mining increases by 12 kg CO 2 e/tonne. In contrast, the same 5% iron ore grade decrease from 20% to 15% would lead to 52 kg CO 2 e/tonne. Thus, …
Description. Iron Ore (fines) Iron ores are rocks and minerals from which metallic iron can be economically extracted. The ores are usually rich in iron oxides and vary in colour from dark grey, bright yellow, deep …
Sinter plants currently have to use many types of ores with different properties owing to the great demand for iron ores, which was driven by the massive growth in Chinese iron and steel industry. On the other hand, the development of iron ore mines is limited and the quality of iron ores is in a tendency of deterioration.
On the other hand, the iron ore used in this study has a density of 3705 kg/m 3. Therefore, if the same size of the fine was produced, the iron ore was a heavier fine, eventually leading to a larger K c. The other reason is that catalysts are mainly made as mentioned in chap 3.2, while iron ores are particles that come from the nature.
Description. Iron Ore (fines) Iron ores are rocks and minerals from which metallic iron can be economically extracted. The ores are usually rich in iron oxides and vary in colour from dark grey, bright yellow, deep purple, to rusty red. The iron itself is usually found in the form of magnetite (Fe 3 O 4), hematite (Fe 2 O 3), goethite (FeO(OH)), limonite …
In metallurgical processes, fluidized-bed technology is gaining more importance because of its advantages. Processes with H 2-rich and CO-rich reducing gases were developed for the reduction of iron ore fines (e.g. FINEX ®).For improvement of these new technologies, greater knowledge about the chemical kinetics of iron ore …
Implementing flue gas recirculation brings changes to gas conditions across the sintering bed, significantly influencing the mineralisation behaviours. Compared with …
Like other sintering processes, iron ore sintering converts iron ore fines of often − 8 mm sizing into larger agglomerates, namely, sinter, between 5 and 50 mm particle size, which possess the physical and metallurgical characteristics and gas permeability required for efficient blast furnace operation.As shown in Figure 14.1, iron ore sintering …
Download scientific diagram | Effect of iron ore fines on the composition of export gas and total amount of iron bearing materials from publication: Optimum Process Conditions for the Production ...
Weighting material such as barite, iron-ore fines used for the preparation of high-density water based drilling fluid because of its high density and well wettability.
To increase the usage of available raw materials, the Ministry of Steel has directed integrated steel players to make use of iron ore fines in steel making after its beneficiation. Advertisement. Republic Business. R.Bharat. Republic World. R.Bangla. R.Kannada. Home. Economy. Live TV. Markets. News. Companies. Auto. Money.
The present paper first describes the methods for testing the metallurgical properties of iron ores, which use a small volume of sample mainly focusing on …
State Key Laboratory of Advanced Metallurgy, University of Science and Technology Beijing, Beijing 100083, China. Tangshan Iron and Steel Co., Ltd., Tangshan 063016, China
In metallurgical processes, fluidized-bed technology is gaining more importance because of its advantages. Processes with H 2-rich and CO-rich reducing …
The feasibility of producing direct reduced iron from cold-bonded, self-reducing composite pellets, constituted from beneficiated iron ore slime, coke, and different binders (dextrin, bentonite, calcium lignosulfonate, and carboxymethyl-cellulose [CMC]) was studied. This was done using a design of experiments approach.
حقوق النشر © 2024.Artom كل الحقوق محفوظة.خريطة الموقع