Ball Mill Success: A Step-by-Step Guide to …
Ball milling is a mechanical process used for the grinding and blending of materials to create finer particles. In this process, a powder mixture is placed in a rotating drum, along with grinding media such as …
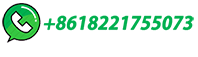