A study on the effect of parameters in stirred ball milling
In this paper, four important parameters of the Drais stirred ball mill, i.e., the bead density, slurry density, mill speed, and the effect of dispersant were selected for investigation. The experimental work was based on a factorial design and 27 milling tests were conducted. It is found that the bead density has an optimum value of 3.7 g/cc ...
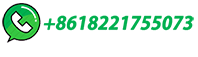