Mechanisms in oxidation and sintering of magnetite iron ore green pellets
In the present work, oxidation and sintering mechanisms in iron ore green pellets under non-sintering and sintering conditions were studied. The intent was to get more information about the sensitivity of the formation of duplex structures for variations in raw material fineness and in green pellet porosity. 2. Materials and methods2.1.
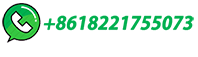