Alternative to deal with high level of fine materials in iron ore
Nowadays, as the demand for iron ore increases together with the depletion of high grade ore deposits, mining companies have been investing to produce iron ore concentrates, such as pellet feeds (95% lower than 0.15 mm) with low level of contaminants.It is well-known that its lower particle size negatively affects the …
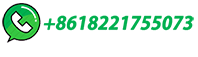