7 Environmental Impacts of Iron Ore Mining
Steel production uses over 98% of the iron ore available on the global market. Iron ore is a significant material that is used to extract metallic iron. Due to the increasing demand for metals, mining, and processing must be done continuously, producing a lot of liquid and solid waste. Massive amounts of tailings containing dangerous elements, including Fe, …
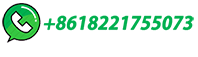