Premium cement milling process For Industries
The cement milling process are designed for cement production efficacy. All categories. Featured selections. Trade Assurance. Buyer Central. Help Center. Get the app.
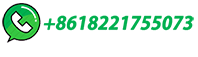
The cement milling process are designed for cement production efficacy. All categories. Featured selections. Trade Assurance. Buyer Central. Help Center. Get the app.
And high cement temperature will cause gypsum dehydration, affect the comprehensive performance of cement, easily lead to the process admixture volatilization in concrete mixing. If we properly reduce the cement fineness requirements, shorten the material grinding time is the most direct way. ... AGICO Cement Ball Mill & Cement EPC Project.
13 Ball Mill - Study & Data 105 14 Ball Mill Formulas 111 15 BIS Specification of Additives 113 16 Cement Testing 115 17 BIS Specifications for various Cements 120 18 Thermo Physical Properties of Different Insulating Materials 124 19 Environmental Standards (Stack, Ambient Air and Water) 125 20 CO
Raw material blending is an important process affecting cement quality. The aim of this process is to mix a variety of materials such as limestone, shale (clay), sandstone and iron to produce ...
Ball mills are tube mills used for grinding materials like cement and involve several components. The document discusses the movement of grinding media in ball mills, optimal ball charge and filling levels, key components like linings, diaphragms, drives and bearings, and factors that influence mill operation such as ventilation, water injection …
Concrete milling, also known as asphalt milling or pavement milling, is a process that involves the removal of a layer of a concrete surface. The goal is to smooth out the surface, correct irregularities, or prepare the surface for a new application, such as adding a fresh layer of asphalt, paint, or coatings.
With years of experience in the cement and over 3000 mills sold worldwide, FL Cement continues to develop its range of efficient milling and grinding solutions. This experience and know-how, as well as close collaboration with our customers, means we can deliver best-in-class technology.
Decrease your maintenance downtime and improve and promote health and safety, with established engineering solutions and optimised components. FL is a worldwide supplier of roller press HGPR and HRP technology using technology based on field-proven components used in 60+ installations dating back to the mid 1980's.
This document discusses Portland cement and the cement manufacturing process. It begins with an overview of what cement is and how it is used to make concrete. It then describes the industrial process for manufacturing cement, involving grinding raw materials like limestone and clay at high temperatures in a kiln to form …
Cement manufacturing - brief description of a cement mill. Cement clinker is usually ground using a ball mill. This is essentially a large rotating drum containing grinding media - normally steel balls. ... However, reading an article or two is perhaps not the best way to get a clear picture of a complex process like cement production.
It is still a challenge to overcome the extended setting process of pure Ca-silicate as root canal fillers. We investigated the effects of attapulgite (a basic hydrous silicate of magnesium and aluminum) and ball-milling liquid medium on the self-curing properties of conventional β-dicalcium silicate (C2Si)-based cements.
The stockpile consists of 40,000 to 60,000 tons of crushed limestone, the primary raw material in the cement manufacturing process. Raw Grinding. Our 310-ton-per-hour roller mill uses waste heat from the kilns to dry the limestone and shale during the raw grinding process. Three 31-ton rolls are positioned vertically and tangent to the grinding ...
Cement milling is the process of grinding together cement clinker, gypsum and other additives to produce a fine grey powder. The resulting material, called "cement meal", is then heated in a rotary kiln to around 2,000°F to produce the finished product known as Portland cement, which can be used for many different construction purposes.
With precise process control, you can optimize the ultrasonic milling process to your target cement particle size and highest energy efficiency. Additionally, Hielscher sonicators are scalable and versatile, available in …
Chemical process industries are running under severe constraints, and it is essential to maintain the end-product quality under disturbances. Maintaining the product quality in the cement grinding process in the presence of clinker heterogeneity is a challenging task. The model predictive controller (MPC) poses a viable solution to …
The finish mill system in cement manufacturing is the second to last major stage in the process, where the feed material is reduced in size from as large as several centimeters in diameter, down ...
For over 60 years technological additives used in process of grinding cement. Application of cement grinding aids can improve performance of ball mills, reduce specific energy consumption, and ...
FL Cement is a technology and service supplier with a passion to help our customers produce cement efficiently. After 140+ years of pioneering new innovations, we are uniquely positioned to be at the forefront of our industry's green transition. ... an interview with Christopher Ashworth Advanced process control contributes to ...
1. SBM Cement manufacturing process milling machine Cement manufacture process milling machine: Ball-mill for cement manufacture process Vertical mill for cement manufacture process Cement in powder form can be changed from plasticity paste to hard stone-like body and can become a total cemented granular …
Cement - Extraction, Processing, Manufacturing: Raw materials employed in the manufacture of cement are extracted by quarrying in the case of hard rocks such as limestones, slates, and …
In cement industry, the control of the milling process has remained a challenging problem for years because of the existing model uncertainties, nonlinearities, changes in the parameters and their interdependence. Cement milling is also a highly energy-consuming operation in the cement industry.
The cement milling process is a critical step in cement production that involves grinding and blending materials to create the final product. The purpose of cement milling is to …
The finish mill system in cement manufacturing is the second to last major stage in the process, where the feed material is reduced in size from as large as …
Part Three: Raw Mill. Process of Raw Mill The proportioned raw material is feed first to a grinding mill. In the mill, particles ground in to very fine sizes. In the grinding unit, drying, grinding and mixing takes place simultaneously. Hot gas from clinker burning unit is passed into the grinding unit to assist the drying and grinding process.
Cement Milling is the last stage in the cement manufacturing process where the quality of the product can be modified / altered / improved as per demands of customers and specification …
The range includes ordinary portland cement, portland blast furnace slag cement, portland pozzalana cement, white cement, ready mix concrete, building products and a host of other building solutions. In ultratech cement hirmi,balodabazar .the cement produced are: 1) OPC 43 - ordinary Portland cement 2) PPC – Portland pozzolana …
the milling process takes place during rotation as a result of the transfer of kinetic . ... Mill. – Cement and Concrete Research, V ol. 33, 2003, 439-445. 16. D i n g, B. C. Modern Predictive ...
For more than 100 years, FL has been delivering cement kilns that are tested, reliable, and require minimal energy and space. Our cement rotary kilns deliver high production capacity with long lifespans and low maintenance. And now, with online condition monitoring services, we can optimise kiln performance even further and help …
Cement manufacturing -brief description of a cement mill. Cement clinker is usually ground using a ball mill. This is essentially a large rotating drum containing grinding media - normally steel balls. As the drum rotates, the …
Based on a dynamical model of the grinding process in closed circuit mills, efficient efforts have been made to optimize PID controllers of cement milling. The process simulation is combined with an autoregressive …
حقوق النشر © 2024.Artom كل الحقوق محفوظة.خريطة الموقع