What is the definition of crushing in mining?
The crushing process is a crucial step in the overall mining operation, as it helps to prepare the ore for further processing. crushing for mining. There are various methods of crushing, and the ...
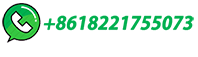
The crushing process is a crucial step in the overall mining operation, as it helps to prepare the ore for further processing. crushing for mining. There are various methods of crushing, and the ...
Crushing is the first step of mineral processing where the ore/rocks from the mine site is fed into the mechanical equipment in order to reduce the size of masses for subsequent usage by ...
After crushing, the ore is screened to remove any impurities before being transported to the steel mill. At the steel mill, the iron ore is melted down and combined with other materials to make steel.
The most common ore crusher for aluminum is a jaw crusher. It is often used in mining and metallurgical processes. A jaw crusher works by using compressive force to reduce the size of large rocks ...
A crusher is a machine designed to reduce the size of Run of Mine (ROM) large rocks to smaller rocks, gravel, sand, or rock dust; this is essential for efficient transport of the ore via conveyors etc. Crushing is the first of …
crushing process. The design of our certifi ed wear parts starts with CAD simulations of the crusher cavity, which is the heart of the crush-ing process. By computer based …
Ore dressing or separation technics have been introduced long ago and had been undergone through huge transformations. ... Crushing and grinding are known as comminution procedure where the major ...
The ore from the feeder next passes over a roll or vibrating grizzly. For the small 150 to 200 ton per day mill this opening can be 2 inches. This will allow the wet sticky fines to pass through the grizzly. A …
Crushing in Mineral Processing. In mineral processing or metallurgy, the first stage of comminution is crushing. Depending of the …
The factors governing the determination of capacity for any open circuit crushing stage are much the same as those we outlined in connection with the secondary stage. In a properly designed crushing plant, excepting those plants which by-pass a portion of the pit-run around the head end of the flow line and inject this fraction back …
Ore is a term used to describe an aggregate of minerals from which a valuable constituent, especially a metal, can be profitably mined and extracted. Most rock deposits contain metals or minerals, but when the concentration of valuable minerals or metals is too low to justify mining, it is considered a waste or gangue material. ... In order to ...
In the limestone ore processing, the crushing machinery is necessary. There are several stages in the crushing process, and the type of machinery used in each stage depends on the characteristics ...
The crushing of ore by steel ball is a random crushing, and the crushing efficiency is very low. Some researches have pointed out that the crushing efficiency of the ball mill is only 6% to 9%. It can be seen that the grinding grain size has a great influence on the mill. In order to achieve the final grinding fineness, it will inevitably ...
The waste from an ore-crushing plant can include crushed rock, soil, dust, and other material that is produced during the process of crushing the ore. Jaw crusher and Cone crusher The waste from ...
The raw ore crushing process is the initial stage of mineral processing, which involves breaking the raw ore into smaller pieces in order to extract valuable minerals. This process may vary ...
Crushing and screening. Iron ore of merchantable grade must be properly sized prior to charging to the blast furnace. Present blast furnace technology commonly requires crushing and screening of direct charge lump ore finer than 10 mm and coarser than 30 mm. The specific size selected is based on the characteristics of the ore and is …
Crushing is the process of size reduction of ore. Size reduction process begins with usage of explosives at the area for production of ore. In later stages, the size reduction process performed with crushers before …
Ore mining can have several environmental and social impacts, including: 1.Deforestation and habitat destruction: Large areas of land are often cleared to make way for mining operations, which can ...
3.2.1 Crushing Equipment. Primary Crushers – Jaw and Gyratory. Within the crushing circuit, a primary crusher reduces material down to a size that can be conveyed and fed …
Atrition crushing is great for the production of very fine particle sizes and it is commonly used in mineral processing and mining for grinding ore. Shear Crushing: Shear crushing takes a shearing force and applies it to the material, which results in the formation of cracks on the weak planes. This method is not frequently used in rock ...
Definition of primary crushing. In ore dressing, the first stage in which crushers take run-of-mine ore and reduce it to a size small enough to be taken by the next crusher in the series. Ordinarily, the Blake jaw crusher or a …
For example, if it is calculated that one trainload if rock will be de live red to the plant each one-half hour, on the average, and our primary crusher has been chosen with a view to getting this tram through in ten minutes, then we must, enviously. either provide stage crushing to match the high capacity of the primary or, if we want to get ...
A washing section is a "must" in all operations handling wet, sticky ore. This facilitates ore handling, crushing, and also affords a means for separation of primary slimes and increasing grinding capacity. These slimes usually contain the bulk of the soluble salts and in many cases this fraction should be treated separately or even ...
4. Hammer Crusher: This is another secondary crusher that is used for crushing brittle materials such as iron ore. It uses a rotating hammer to break the ore into small pieces. 5. Roll Crusher ...
Run of mine material is transferred into a gyratory crusher's upper-level hopper. The walls of the gyratory crusher's hopper are lined with "V-shaped" pieces, the mantle and the concave, like a jaw crusher but shaped like a cone. The ore is discharged through the smaller bottom output hole of the cone.
The Iron Ore Crushing Plants are developed according to Baichy series iron ore crushing equipment's design idea, which expands the concept field of coarse crushing and fine crushing. Iron ore crusher is designed based on the conception of fully adapting various iron crushing condition. This series iron ore crusher plant really …
The grinding process in mining refers to the reduction of the size of ore or rock particles by mechanical means to facilitate the extraction of valuable minerals. It is a crucial step in the ...
Crushed Ores are obtained from crushing various items. If making a Precision Mechanism fails, there is a small chance to receive Crushed Gold Ore, thus making it renewable. 0.4: Removed Crushed Brass Removed …
Iron ore crushing processes typically involve several stages of crushing and screening to achieve the desired size and specification for further processing. The equipment used in these processes ...
Crushing and screening are two essential processes in the mining, quarrying, and construction industries. ... Crushers can be used to reduce the size of raw materials such as rocks, ore, and coal ...
حقوق النشر © 2024.Artom كل الحقوق محفوظة.خريطة الموقع