Effect of Iron Phase Evolution on Copper Separation from Slag
Copper slag, a by-product of copper pyrometallurgy, inevitably contains a certain amount of copper. Oxygen-enriched smelting technologies increase the copper …
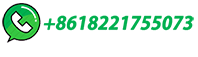
Copper slag, a by-product of copper pyrometallurgy, inevitably contains a certain amount of copper. Oxygen-enriched smelting technologies increase the copper …
Iron grain growth during deep reduction roasting is important for iron enrichment from copper slag (CS) through magnetic separation. In this work, a novel method of additive-free activation roasting, including oxidation and subsequent reduction roasting, was proposed to increase the iron grain size, then the iron was extracted by …
The separation is much better than the customary one with 3.5M hydroc … Iron(III) can be separated from copper(II) and many other elements by eluting these from a column of AG1-X4 anion-exchange resin with 8M hydrochloric acid, while iron(III) is retained and can be eluted with 0.1M hydrochloric acid. The separation is much better than the ...
Recovery of value-added products from copper slag by pyrometallurgy: Transfer and structure of arsenic compounds ... little is actually consumed and the metal resources cannot be effectively utilized [1]. In recent years, to recover copper and iron, the flotation method has been widely used in industry, but a large number of flotation tailings ...
Pyrometallurgical process is one that involves a high temperature (above 1200 °C) smelting process to break down and treat spent battery materials (Fig. 1 A) (Georgi-Maschler et al., 2012).Essentially, spent LIBs are burnt in a furnace without any kind of pretreatment steps. Their components are broken down into subcomponents while …
Water-cooled tap holes are used to withdraw molten metal-bearing material into a settling furnace to allow separation of the matte and slag phases. ... slag layer …
As the world's largest producer of refined copper, China accounts for about 1/3 of the world's production. At present, China's refined copper is mainly produced by pyrometallurgy [1,2,3].The annual discharge of copper slag exceeds 10 million tons according to the calculation of 2.2 tons of copper slag per ton of refined copper …
categories: pyrometallurgy, hydr ometallurgy, and electrometallurgy. Historically, pyrometallurgy employs high temp eratures to carry out smelting and refining. operations to extract metals from ...
A plot of the temperature dependences of the free energies of these reactions, superimposed on similar plots for the oxygen removal reactions (ref{2.4}) is called an Ellingham diagram (Figure (PageIndex{2})). …
China's copper resources are characterized by low grade and complex composition. A large amount of copper smelting slag (CSS) containing valuable elements such as copper and iron is produced through smelting. With the increasing shortage of copper resources, the full recovery of valuable elements in CSS plays an important part …
There are several major megatrends having an impact on pyrometallurgical metal processing. The steadily growing demand for all metals is strengthened by the emergence of electrical vehicles (EV), which brings …
Pyrometallurgy treatment of electroplating ... zinc, chromium and copper, were commonly occupied by 0.5–5% of the sludge. Such metals were unbiodegradable, and easily transported with the ... Among the separated spinel, the Zn content was 40.0%, iron content was 34.8% and aluminum content was 12.8% (Fig. 2 c), apparently higher than …
During the reduction roasting, additive CaO reacted with Fe 2 SiO 4 of copper slag, forming CaO·SiO 2 and 2CaO·SiO 2, which ameliorates the separation between iron and other minerals during magnetic separation. Meanwhile, additive CaF 2 improved the growth of iron grains, increasing the iron grade and iron recovery. The …
In the second phase of the process the partial pressure of sulphur dioxide is considered to be maintained at 0.1 atm. Figure II.13.2 shows the calculated relationship between the amounts of iron and sulphur in the matte under these chosen conditions. The relationship between these two variables is a function of the composition of the slag and …
The process starts with physical separation of metals from other constituents of the wastes. Once separated the metallic constituents mainly consists of iron, aluminum, copper, lead, tin, antimony, zinc, and precious metals. During copper smelting the metallic constituents are fed to the furnace where they are heated to their molten state.
Blast furnace has been used for iron/copper/copper -nickel/zinc/lead and zinc-lead complex concentrate smelting for a long time. It plays a fundamental role to modern metallurgy Feature > ... (Distillation …
There appears to be a two-stage leaching process (Fig. S3†) with the first stage (H 2 SO 4) serving to remove selectively iron and copper impurities and the second stage in HCl solution allowing the separation of Ni and …
About 80% of the primary copper production comes from pyrometallurgical treatment of copper ores (Potysz et al., 2015;Gbor et al., 2000;Sarfo et al., 2017).
The copper rod is hot-rolled and then surface treatment for cooling and reduction. The system can use electrowon copper cathode or high grade copper scrap (≥99.5) as raw material to directly get electrical grade copper rod, from which copper scrap is highly efficient recycled.
The waste valorization via selective membrane separation, membrane distillation crystallization (MDC) and reverse electrodialysis (RED) was a Chile case study due to high activities of copper mining.
Synchronous extractions of nickel, copper, and cobalt by selective chlorinating roasting and water leaching to low–grade nickel–copper matte. Separation and Purification Technology 195, 149 ...
Dissolved copper will plate out on an iron surface due to the following reaction: Cu+2(aq) + Fe(s) ===> Fe+2(aq) + Cu(s) So, if a solution with dissolved copper is run through a …
Pyrometallurgy has existed in one form or another for several thousand years. From paintings on the walls of ancient Egyptians, we know that the idea of …
The former contains more iron (Fe), less magnesium (Mg), about 1% of nickel, and a certain amount of cobalt, which is suitable for hydrometallurgy, such as high-pressured acid leaching. The latter has more magnesium, less iron, about 2% nickel, and low cobalt content, which is suitable for pyrometallurgy, such as rotary kiln-ore furnace.
A novel technology, modified roasting in CO–CO2 mixed gas and magnetic separation, was presented to recover iron from copper slag. The effects of various parameters such as dosage of flux (CaO), gas flowrate of CO and CO2, roasting temperature, roasting time, particle size of modified slag and magnetic flux density on …
In this study, a novel method to recover copper, zinc and iron from copper slag by SO 2 –O 2 roasting-leaching-magnetic separation was proposed. The effect of roasting experiment conditions were roasting temperature of 900 °C, holding time of 120 min, and φ SO2 (The volume fraction of SO 2 in the mixed gas of SO 2 and O 2) of …
The main difference between the PLS after bioleaching and acid leaching is the Fe content. The microorganisms used in bioleaching are primarily iron-oxidizing and sulfur-oxidizing bacteria, and 9 K medium is a well-known medium for their cultivation [20], [35]. 9 K medium contains a significant amount of Fe, approximately 8.8 g/L.Therefore, it …
9 rowsIndustrial grade pyrometallurgy is usually direct put the WPCBs containing 5%–40% copper into the blast furnace, and the product is black copper containing …
discovered that heat made copper more malle-able. Casting and smelting of copper began around 4000-3500 B.C. (see figure 6-2). About 2500 B. C., copper was combined with tin to make bronze—an alloy that allowed stronger weapons and tools. Brass, an alloy of copper and zinc, probably was not developed until 300 A.D.
Metal recovery methods from CS can be mainly divided into pyrometallurgy and hydrometallurgy. Traditional Pyrometallurgy methods include using coke as a …
حقوق النشر © 2024.Artom كل الحقوق محفوظة.خريطة الموقع