Tungsten-tin ore beneficiation process design and it's …
In order to improve the quality of tungsten and tin concentrates, comprehensive recovery of associated useful minerals, in the selection section, depending on the nature of the ore, generally regrind the middle ore, secondary concentrate and concentrate respectively, and then use the combined process of re-election, flotation, …
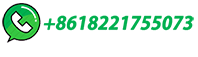