Recycling of iron ore tailings into magnetic nanoparticles …
Iron ore tailing is a major solid waste requiring advanced recycling methods because ore tailing powder is polluting air and water resources. For instance, about 300 million tons …
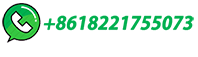
Iron ore tailing is a major solid waste requiring advanced recycling methods because ore tailing powder is polluting air and water resources. For instance, about 300 million tons …
low-grade from high-grade ore in the process. Silica levels, which range from 14% to 20% in the barren ore, have reduced to 6.4% after processing; while alumina levels, which range from 5.9% to 8.8%, have reduced to 2.8% after processing. The iron ore wash plant also removes clays from. the feed material, with the combined effect
The characteristics of iron minerals in cyanidation tailings with a low iron grade were determined via chemical composition analysis, iron phase analysis, and mineral liberation analysis (MLA). The results …
The Falconbridge and Inco pyrrhotite processing plants have been closed since 1972been closed since and 1982been closed since, respectively (Rezaei et al. 2017, whilst the pyrite roaster at the ...
Our end-to-end tailings processing solutions process help our customers deliver quality commodities that align with their business objectives. Iron Duke – Iron Ore Tailings; Iron Baron – Iron Ore Tailings; Samancor – …
1. Introduction. Mining, mineral processing, and extractive metallurgy are essential industries for metal production but generate huge amounts of tailings [].Mine tailings are by-products of separating valuable minerals from uneconomic materials [2,3] and are generally deposited in open-air tailings impoundments without any treatments …
Experimental Study of the Sulphatizing Roasting of Flotation Tailings from Copper Slag Processing Using Iron Sulfates. ... Podjelnikova E S and Dyubanov V G 2020 Research on the Process of Sulphatizing Roasting of Copper Slag Flotation Tailings Using Iron Sulphates IOP Conf. Ser. Earth Environ. Sci. 459 042004. Google Scholar. Export …
Iron ore tailings (IOTs) are a form of solid waste produced during the beneficiation process of iron ore concentrate. In this paper, iron recovery from IOTs was …
In Sivas-Divriǧi Iron Ore Concentrator 600,000 tons of tailings is discarded annually. There are already one million tons of tailings deposited in the ponds from the previous production activities.
Given the moderate quantity of iron oxides within the material and the similarities of these tailings with phosphate ores, the evaluation of the Crago flotation process emerged as an interesting approach to recover valuable minerals from the finest fraction of Mont-Wright's tailings (Silva et al., 2022).
This work aims to evaluate the use of a superabsorbent polymer (SAP) to provide improvements in the handling properties of iron ore tailings (IOT). The material studied came from the magnetic separation reprocessing of the material discarded at the Gelado Dam, located in Serra dos Carajás in the state of Pará, Brazil. While the …
Iron tailings re-processing technology is one of the important methods for reusing iron tailings. Different types of iron tailings contain different types of valuable minerals, and the recycling methods used are also quite different. Common valuable minerals in iron tailings mainly include hematite, limonite, hematite, ilmenite, …
The Arequipa region has the third largest mining industry in Peru, producing 19.5 % of the country's annual gold in 2022 (Vera Gargurevich et al., 2023).Small-scale gold processing facilities (ore capacities up to 350 metric tons per day) play a large role in the industry, accounting for 40 % of the Arequipa region's gold production, with medium- …
Iron tailings, generated from the beneficiation and metallurgy of iron ore, are hazardous wastes that pose significant environmental challenges due to their large …
With advent of novel technologies, mining companies are now figuring out ways to extract valuable metals from tailings. In gold, copper sulfide and iron ore tailings, the potential of extracting minerals is an opportunity. Reprocessing tailings to collect the valuable minerals can be a cost-effective approach compared to processing …
In recent years, with the rapid development of the iron and steel industry, the amount of industrial waste gases, wastewater, and waste residues has increased every …
This paper deals with a systematic research on preparation and utilization of tourmaline from tailings of an iron ore processing plant in Xinjiang, China. Tourmaline has the characteristics of piezoelectricity, thermoelectricity, spontaneous polarization and far-off infrared radiations. Ultra-fine powders of tourmaline have extensive ...
Rapid economic development and increased demand for mineral products in China have led to extensive extraction of various ores, resulting in significant environmental challenges associated with the generation of industrial solid waste, particularly iron tailings. Despite being a major mining nation, China faces issues of wasteful practices, …
Publish Date: 25 June 2022. Abstract. Iron tailings is one of the main solid waste produced in the process of iron ore development, and is also an important secondary resource. The common ways of comprehensive …
Direct reduction refers to the process of reducing iron minerals in copper slag to metallic iron particles below the melting temperature of copper slag [].Using direct reduction–magnetic separation technology to recover iron resources in copper slag has fair recovery effect and short reaction time, which is the development trend of …
For ferruginous quartzite of the Mikhailovsk deposit, the features of mineral composition, iron occurrence, granulometric composition, and opening of phases of stage and total tailings of processing are considered. Extraction of hematite from tailings using combined concentration schemes is one of the variants of complex utilization of mineral source in …
The tailings from the re-processing plant will be re-deposited in a new area far from urbanization, allowing for the rehabilitation of the real estate currently occupied by these historic tailings. The first step in the process involves a mild-regrind and mild acid leach of the tailings (pH 2.5 to 3.0) to dissolve up to 40% of the uranium.
Iron ore tailings (IOTs) are a form of solid waste produced during the beneficiation process of iron ore concentrate. In this paper, iron recovery from IOTs was studied at different points during a process involving pre-concentration followed by direct reduction and magnetic separation. Then, slag-tailing concrete composite admixtures …
Tailings are waste generated during the mineral processing process and are the main component of industrial solid waste. Iron tailings are one of the largest ore types. If iron tailings are not properly treated, they will cause many hazards, such as land occupation, environmental pollution, safety hazards, etc. Therefore, reasonable …
04 Iron tailings re-processing technology- the combined separation methods. Sometimes, if applying a single magnetic separation to the iron tailings, the separation power of ultra-fine iron minerals is low after fine grinding, which will make it easy to lose fine iron minerals during the magnetic separation process and affects the grade and ...
Master iron ore tailings disposal with expert tips on analysis, monitoring, and environmental compliance.
The S2 tailings have a fines content (FC) of 33.3% and a specific weight (G s) of 2.97. This feature is associated with the process of iron ore beneficiation for the different tailings. When there are more fines in the tailings, iron recovery becomes more difficult and consequently, the iron content and specific weight of this material will be ...
The integrated utilization efficiency of the iron tailings reelection process is low, and the general treatment method for iron tailings is stacking in tailings dams, which pollutes the environment and results in safety accidents; moreover, the construction of iron ore tailings ponds requires enormous areas of land, which increases the economic ...
Iron ore tailings (IOTs) are the indusus solid waste discharged by concentrating mills after processing iron ores and selecting "valuable components" (Yao et al., 2020). In China, 600 million tons of …
In addition to this, stringent environmental regulations involved in the opening of new mines and the problems involved in disposal of tailings (slimes), it is the need of the hour to effectively beneficiate low-grade iron ore to make it suitable for iron-making process. The iron ore industries of India are expected to bring new technologies to ...
حقوق النشر © 2024.Artom كل الحقوق محفوظة.خريطة الموقع