Dynamic behavior and separation prediction of magnetic ore …
1. Introduction. The past decades have witnessed tremendous progress made in the magnetic separation technology that have significantly decreased the industrial grade of mined iron ore (Liu et al., 2020, Zeng et al., 2019).However, the extensive energy consumption and high capital costs required in utilization of low-grade …
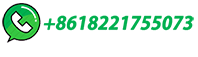