Comparing molecular weight models for polymer degradation with ball
1. Introduction. In the field of polymer mechanochemistry, mechanical forces are applied to polymers, leading to chemical transformations in their chains [1], [2], [3], [4].Various methods can be utilized to conduct polymer mechanochemistry, such as single molecule force spectroscopy [5], ultrasonication [6], and ball-mill grinding (BMG) …
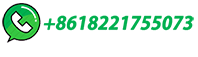