A study on the accretion formation in DRI kilns and …
sponge iron. As the iron ore is in direct contact with the reducing agent throughout the reduction process, it is often termed as direct reduced iron (DRI). Sponge iron is …
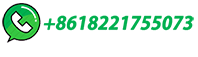
sponge iron. As the iron ore is in direct contact with the reducing agent throughout the reduction process, it is often termed as direct reduced iron (DRI). Sponge iron is …
The rotary kiln consists of a rotating cylindrical shell lined inside with refractory material. The kiln is around 80 ... A 2D CFD model of rotary kiln for sponge iron process is developed in this work and simulated using ANSYS 14.5. The present study discusses the behavior of temperature profile of bed and gas along the length of the kiln …
Present work deals with two design modifications proposed for sponge iron plant. First design accounts for preheating of kiln air using waste gas exiting from ESP. For second design water is heated using hot sponge iron to preheat rotary kiln air. A model is developed to compute coal demand of process based on different factors. For each …
Sponge iron as a special type of zero-valent iron combined with microorganisms to form the biological sponge iron (SFe-M) system. It has obvious benefits in removing refractory pollutants. The optimum parameters based on the production of hydroxyl radicals in the SFe-M system were determined as initial pH 4, SFe dosage of …
It is seen that the growth of sponge iron industry in last few years is unremarkable and today India is the largest producer of sponge iron as it covers 16% of global output. Sponge iron is used as feedstock and a recognized alternative to steel scraps in iron and steel making processes.
In the context of carbon reduction and emission reduction, the new process of electric arc furnace (EAF) steelmaking based on direct hydrogen reduction is an important potential method for the green and sustainable development of the steel industry. Within an electric furnace for the hydrogen-based direct reduction of iron, after …
Contribute to sbmcrushers/sbmchina development by creating an account on GitHub.
Abstract. This book promotes understanding of the raw material selection, refractory design, tailor-made refractory developments, refractory properties, and …
In this study, we firstly develop the photo-Fenton-like system with millimetric sponge iron (s-Fe 0), H 2 O 2, visible light (vis, λ ≥ 420 nm) and rhodamine B (RhB), and present a comprehensive study concerning the mechanism. Thus, we investigate (1) the adsorption of RhB onto s-Fe 0, (2) the photo-Fenton-like removal of RhB over iron …
To enhance the dechlorination reactivity of millimetric sponge iron (s-Fe 0), a facile one-pot method was used to decorate s-Fe 0 with Ag + ions under ambient conditions. The results recorded by X-ray diffraction patterns, X-ray photoelectron spectra and high-resolution transmission electron microscopy demonstrated that the growth of …
In order to find out how much energy can be transferred to the sponge iron particles, the heating process in the silo should be simulated. Sponge iron particles in the silo can be considered as a fixed bed. ... Other advantages of using this method are saving in electrode and refractory consumption, decreasing moisture in EAF feed and reducing ...
The essence of blast furnace ironmaking is the reduction process of iron, that is, coke is used as fuel and reducing agent to convert iron from iron ore or iron-containing raw materials at high ...
In this study, we firstly develop the photo-Fenton-like system with millimetric sponge iron (s-Fe 0), H 2 O 2, visible light (vis, λ ≥ 420 nm) and rhodamine B (RhB), and present a comprehensive study concerning the mechanism. Thus, we investigate (1) the adsorption of RhB onto s-Fe 0, (2) the photo-Fenton-like removal of RhB over iron …
The main products produced by the direct reduction method include solid sponge iron, iron granules and liquid pig iron. Among them, the sponge iron production method is the most mature and has the ...
To date, zero-valent iron (ZVI)-based technique has encountered a baffle, challenging simultaneous detoxification of refractory rhodamine B (RhB) and p-nitrophenol (PNP) possessing strong electronwithdrawing nitro-group.In this study, we synthesized Ag-Cu decorated sponge iron (s-Fe 0)-based trimetal for simultaneous degradation of RhB …
This paper presents an approach to find the best modification in the coal-based sponge iron process with an aim to integrate energy in it. For this purpose, a few energy conservation cases are formulated by integrating unutilized energy present in possible areas of process flow sheet. When unutilized energy of the process is …
The metallic iron in this process is produced by the reduction of iron oxide below the fusion temperature of iron ore (1535 deg C) by utilizing carbonaceous material present in the non-coking coal. As the iron ore is in direct contact with the reducing agent throughout the reduction process, it is often termed as direct reduced iron (DRI).
4.0 Potential Low-carbon Technology Options for Indian Direct Reduction of Iron Sector. 4.1 Direct Reduction of Iron Production Using Solid Coal. 4.2 Direct Reduction of Iron …
Different peroxides always suffer from different factors for controlling their amounts used in Fenton-like systems (Bai et al. 2023, Ji et al. 2018, Pan et al. 2018, Preethi et al. 2024, Subramanian and Prakash 2021).As for H 2 O 2, the large-scale industrial preparation method is mainly based on the ethyl anthraquinone reaction, which is a multi …
Direct Reduction of Iron Process (Sponge Iron Plants). New Delhi: The Energy and Resources Institute Published by The Energy and Resources Institute (TERI) Darbari Seth Block, IHC Complex, Lodhi Road, New Delhi – 110003. iii ENERGY-EFFICIENT TECHNOLOGY OPTIONS FOR DIRECT REDUCTION OF IRON PROCESS
Steelmaking based on direct reduced iron (DRI, and its compacted derivative hot briquetted iron, HBI) is an anticipated important global alternative to current steel production based on FeOx reduction in …
Impurities are removed by the subsequent electric steel process. The sponge iron is melted into the actual crude steel. This process will be discussed in more detail in the next section. In the direct-reduced iron (DRI) process, the iron ores are reduced directly to sponge iron by gaseous reducing agents! Electro-steel process. In …
In subject area: Materials Science. DRI, also known as sponge iron, is the product of reducing iron oxide in the form of iron ore and steel plant wastes into metallic iron, …
Sponge iron (SFe), a typical ZVI material, has high Fe(0) content and large specific surface area, and is a promising alternative electron donor for the degradation of nitroaromatic compounds (NACs) [12].It was previously supplemented into activated sludge to form a biological sponge iron (bio-SFe) system to enhance treatment effects in …
This process involves three stages, which are as follows: the first one is the reduction of iron ore to produce sponge iron also called Direct Reduced Iron (DRI), which takes place in a direct reduction reactor; the second one is the gasification of petroleum coke with the DRI smelting and takes place in a gasifier furnace, and the third one is ...
To enhance the catalytic reactivity of millimeter-scale particles of sponge iron (s-Fe 0), Cu 2+ ions were deposited on the surface of s-Fe 0 using a simple direct reduction reaction, and the catalytic properties of the bimetallic system was tested for removal of rhodamine B (RhB) from an aqueous solution.The influence of Cu 0 loading, …
India produces one-third of the global sponge iron, mostly from rotary kilns using coal as an energy source, resulting in higher energy and emission intensities than the global …
the refractory pores and causes exsolution of t he end members of the system. Accretion build up. in the Sponge Iron kiln can not be e liminated since it originates from the input constituents of ...
The conventional iron and steel industry (ISI), driven by coal utilization as its predominant feedstock, constitutes a substantial source of greenhouse gas emissions. Hydrogen metallurgy presents the opportunity to mitigate carbon emissions in ISI from the origin. Among hydrogen metallurgical approaches, the hydrogen-based direct reduction …
Coal saving through unique refractory design. 100 TPD DRI Kiln refractory lining done in dual layer in Mahendra Sponge and Power Ltd.
حقوق النشر © 2024.Artom كل الحقوق محفوظة.خريطة الموقع