A comprehensive review of the application of plasma …
The gasifier reactor shell is attached with a slag removal system at the bottom to remove slag continuously. The syngas flows from the upper portion and enters the water …
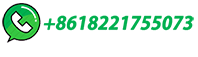
The gasifier reactor shell is attached with a slag removal system at the bottom to remove slag continuously. The syngas flows from the upper portion and enters the water …
A two-stage fixed-bed reactor has been employed to simulate elements of tar cracking in a downdraft gasifier. In this reactor, tar is generated by pyrolysis in the first stage and cracking and ...
The gasifier is a throated downdraft reactor with a height of 50 cm and a diameter of 31 cm at the drying zone, whereas the diameters at the throat section and at the end of reduction zone are 16 cm and 25 cm, respectively (see Fig. 3) and with a height difference of 25 cm above the grate. The gasifier height is divided equally with a step …
This Gasifier is atmospheric Fluidized Bed Gasifier Biomass feed into Gasifier Reactor by screw conveyor. Air inlet to gasifier reactor by root blower at bottom of gasifier bed passes the multiple air nozzle for uniform air distribution.The fuel gas exit from gasifier reactor is at 700℃ and its composition is (CO, H2, CO2, CH4, N2).Bottom Ash is …
As I said in step 1, a biomass gasifier is a chemical reactor that converts wood, or other biomass substances, into a combustible gas. The formula is simple. Biomass + Heat = Pyrolysis Byproducts. Pyrolysis is a fancy-pants word that chemists use to describe the process of heat breaking down big molecules into smaller ones. In the gasifier we ...
A major disadvantage of this reactor type is that O 2 is trapped in the bubbles, and combustion may take place anywhere in the gasifier, which reduces the …
Bubbling bed gasifier is classified as the oldest reactor in fluidized bed gasifiers [56], [57]. The beds are majorly made up of inert particles such as sand or …
an opening in the hearth plate at the bottom of the gasifier vessel. The product gas leaves from the top, typically at 400 to 500 °C (Minchener, 2005). 6.2.2 downdraft Gasifiers A downdraft gasifier is a co-current reactor where air enters the gasifier at a certain height below the top. The product gas flows downward (giving the name
The Mitsubishi Heavy Industries (MHI) gasification technology was developed with the goal to maximize the gasifier efficiency (e.g., dry feed, and a unique two-stage reactor design) and reduce costs (e.g., air …
The operating conditions for this gasifier are shown in Table 1. Additionally, the stirred-reactor mixing that found in this gasifier separates the extracted ash/char particles from flue gas by a cyclonic device. The process is followed by returning solids into the fluidized bed, forming an internal solid circulation [62].
Gasifier Reactor Design, Hillsborough. 1,137 likes · 23 talking about this. We offer a full range of services in the design, optimisation and procurement of biomass and waste gasfiiers
Numerical identification of flow defects is now possible. ï‚· Highlight of areas that could be optimized. ï‚· Information associated to the mechanical holding of the equipment is provided The GAYA experimental platform in Saint-Fons, France, took into account these results for the final design of the gasifier. a b c Fig. 2 (a) Geometry ...
The gasifier, as shown in Figure 9, is a dry feed, oxygen-blown, top fired reactor with a water wall screen in the gasifier. It is good for a wide variety of feed stocks, from bituminous to low-rank coals.
Figure 2 shows the gasifier reactor, the LPG burner (O 2 cylinder), long cooling pipe and blower fan during startup, while Fig. 4 depicts the gasifier reactor, …
In entrained-flow gasifiers, ... The slurry feed is a simpler operation, but it introduces water into the reactor which needs to be evaporated. The result of this additional water is a product syngas with higher H 2 to CO ratio, …
Firstly, conventional reactor definitions are not sufficient given that three reactions (combustion, pyrolysis and gasification) occur in an industrial gasifier. Secondly, variables affecting char reactivity during gasification show that the char surface area is the most complex variable to analyze. Also, single-step kinetic models provide ...
Main types of gasifier reactors [63] Figure 3 shows the various schematics of Updraft, Downdraft, Fluidized Bed and Entrai ned Bed gasifiers [63]. 5.4. Plasma Gasifier.
This reactor was designed according to the principle presented in and it was operated before the tests of this project as an air-blown gasifier to produce fuel gas. The reactor is a refractory-lined pressure vessel with an outer diameter of 1.62 m and an inner reactor diameter of 0.8 m.
gasifier is much smaller than that for other processes, such as char gasification and combustion. So, we assume that coal drying takes place instantaneously at the top of gasifier. 4.2 Coal pyrolysis 4.2.1 Pyrolysis reaction Coal pyrolysis is to break the coal to form the products of CO, H2, CO2, H2O,
All of the gasifiers discussed above fall into basically four primary gasifier configurations: moving bed, fluidized bed, entrained flow and transport as shown in Figure 18. Each of these is defined on how …
These are well-mixed reactors operating with lower peak temperatures than the plug flow reactors. These gasifiers have coal residence intermediate between the …
NOTAR® reactor is the sole industrial gasifier producing a CLEAN SYNGAS (NO – TAR!) at the outlet of the reactor. » Technology lies on the physical separation of the reaction zones » Design allows accurate control of critical reaction parameters » Gasifiers assembles 3 reaction zones into a compact reactor
A crossdraft gasifier is a cocurrent moving-bed reactor, in which the fuel is fed from the top and air is injected through a nozzle from the side (Figure 8.7) of the gasifier. It is primarily used for gasification of charcoal with very low ash content. Unlike the downdraft and updraft types, it releases the product from its sidewall opposite to ...
The GrabCAD Library offers millions of free CAD designs, CAD files, and 3D models. Join the GrabCAD Community today to gain access and download!
The aim of this study is therefore to design an optimal gasifier reactor for the gasification of crop residues using Integrated Multicriterial Decision Making (MCDM) Techniques and Quality Function Deployment (QFD) methodological approach. The MCDM/QFD framework consists of user requirement, engineering parameters and seven gasifier types.
A downdraft gasifier is a co-current reactor where air enters the gasifier at a certain height below the top. The product gas flows downward (giving the name downdraft) and leaves through a bed of hot ash (Figures 6.4 and 6.5).Since it passes through the high-temperature zone of hot ash, the tar in the product gas finds favorable conditions for cracking (see …
The gasifier is constructed of refractory-lined pipe, which allows less expensive metal to be used in the reactor shell. The gasifier operates at a high solids recirculation rate which results in excellent gas-solids contact in a highly turbulent environment, with high heat and mass transfer rates. The KBR transport gasifier is particularly ...
Gasifier Reactor. The geometric parameters, operating . conditions and the performance characteristics were . determined. It was found that the blower can sufficient ly .
The downdraft gasifier is an appropriate choice for stable and clean syngas production. The size of the reactor can be adjusted during the gasifier design by changing the ratio of height and diameter or the aspect ratio (H/D). Several parameters were investigated in this study: (1) Transient time, (2) Temperature profile, (3) Steady state …
This chapter presents the different categories of gasification reactors as they apply to various types of feedstocks. It focuses on gasifier types, gasifier designs, the process …
حقوق النشر © 2024.Artom كل الحقوق محفوظة.خريطة الموقع