Silica sand processing plant equipment
The production process for silica sand consists of crushing, grinding, sizing, beneficiation, dewatering and drying. can supply complete flowsheets using its own equipment and that of partners. Our planet …
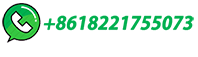
The production process for silica sand consists of crushing, grinding, sizing, beneficiation, dewatering and drying. can supply complete flowsheets using its own equipment and that of partners. Our planet …
The process of making `CO_{2}` sand moulding process starts with mixing fine sand, sodium silicate (up to 5%), a little moisture, adding additives (coal dust, saw flour, dextrin, molasses and husk) and curing the mixture under `CO_{2}` gas until sodium silicate gel gets hard and binds fine dry sand together. ... Silica sand used in this process ...
The physical, mechanical and chemical processing of silica sand, the main ingredient of silicate glass, are routinely carried out in glass and ceramic industries worldwide to enhance the silica ...
Oxidation. Formation of a thin layer of silicon dioxide on wafer surface. 5. Photolithography. Transferring a pattern onto the wafer surface using light and masks. 6. …
Step one is to take high‑purity silica sand, the kind used for glass. (Lump quartz is also sometimes used.) That quartz is then blasted in a powerful electric furnace, creating a chemical ...
Binders are a big part of the core-sand making process. Green sand cores are made from standard damp molding-sand mixtures, and a binder, like dextrin. Cores of this type are very fragile and can be made with an arbor or interior wires to facilitate handling. Dry sand cores do not contain water. They are made from silica sand and a …
High-quality silica sand makes up around three-quarters of the batch of raw materials used in the glassmaking process. The other quarter is made up of soda, limestone, and clarifying agents along with a percentage of recycled glass. The following is the process for making flat glass, which is commonly produced with silica sand.
Ferrous foundries (those dealing with iron and steel) usually use silica sand, sometimes known as quartz sand. Silica sand has long been used in core making, so switching to using the same aggregate …
It shows that specimen S1 having compositions of 50% of low-density polyethylene and 50% silica sand particles, has a minimum wear rate of 0.143 × 10 –8 kg/m, which reveals the incorporation of ...
Step1:Pattern & Core Making. Wooden, plastic, or metal patterns create the mold cavity. Sand cores form internal features like holes. Care in Pattern Making: Consider pattern material, geometry, …
High-grade silica in glass making. To produce glass sands, a more refined sand is required than the common construction sand used for concrete. ... Guaranteed precision and maximum process efficiency – the precision of the cut points and careful attention to all material transfer points maximises retention of in spec material and water within ...
To make sand melt, you need to heat it to roughly 1700°C (3090°F), which is approximately the same temperature a space shuttle reaches as it re-enters earth's atmosphere. The sand commonly used to make glass is comprised of small grains of quartz crystals, made up of molecules of silicon dioxide, which is also known as silica. When those ...
Silica sand is often utilized for its purity and properties; however, other varieties with differing mineral makeups can also be helpful. How does silica sand contribute to the glass recycling process? Silica …
Sand is composed of silica (also known as silicon dioxide), and is the starting point for making a processor. Sand used in the building industry is often yellow, orange or red due to impurities, but the type …
Borosilicate glass is created when boric oxide, silica sand, soda ash, and alumina are combined in a melting medium. Desert sand has a very narrow range of rounded quartz grains. Masonry sand is a type of fine-grained sand used in the manufacture of concrete and mortar. ... Can You Make Glass Out Of Any Type Of …
The green sand mould Green sand moulds are made using a moist, clay-bonded sand, alongside various other additives. Typical green sand moulds contain a base sand, usually a high-silica (SiO 2) sand with a clay bonding material (bentonite) and water.. The sand grains themselves should be relatively spherical to facilitate flow and compaction of the …
Sand casting is a metal casting process that uses sand as the primary molding material. It is one of the oldest and most widely used casting methods due to its versatility, flexibility, and cost-effectiveness. …
Besides, the wet sand making process has a long sand dewatering cycle, requires a large sand silo, will affect the output of finished sand. The wet process brings environmental pollution caused by production wastewater. High water consumption, but low recycle rate. The moisture content of the finished sand is not easy to control below 6%.
The following is the process for making flat glass, which is commonly produced with silica sand. Batched – The main components, including the silica sand, limestone, soda, and recycled glass, are …
Quartzite comes from ancient deposits of quartz sands that formed sedimentary deposits. Over time and with heat and pressure, these quartz sandstones were transformed into the metamorphic rock ...
The silica sand manufacturing process. … It is the first choice equipment for artificial sand making and the stone reshaping. (1)Large capacity, …
Installation Process of Pavers Using Silica Sand for Paver Installation. When we choose to use silica sand for paver installation, we opt for a traditional yet effective method. Silica sand is easy to work with, …
The sand-casting process has been the mainstay of foundry processes for millennia. Although a mature process, improvements continue to be made, assuring that this …
Abstract. To produce high-purity silica sand usable for glass making, the present study was carried out. The objective of this work was to increase the silicon dioxide (SiO 2) content to at least 99% using a simple process without chemical input.The raw sand samples were taken from the Ivorian sedimentary basin, from Maféré and Assinie areas, …
Purification starts by heating the sand with a reducing agent, carbon, to produce carbon monoxide and silicon. The product of this process, known as metallurgical grade silicon (MG-Si), may be as much …
Alkali metal ions are easily dissociated in water, making the zero electric point of feldspar lower than that of quartz sand, thus realizing the silica sand flotation separation process. 3. Flotation separation of …
Sand / Ingot Sand Silicon is the second most abundant element in the earth's crust. Common sand has a high percentage of silicon. Silicon – the starting material for computer chips – is a semiconductor, meaning that it can be readily turned into an excellent conductor or an insulator of electricity, by the introduction of minor amounts of
What is Silica Sand? Silica sand, which can also be called industrial sand, white sand, or quartz sand, is mainly made up of oxygen and silica. In glass manufacturing, it can simply be called "sand" for making glass, since this is its main use. Sand must have at least 95% SiO2 and less than 0.6% iron oxide to be classified as …
Making glass is a very ancient process, with archaeological evidence of glass making dating back to before 2500 BC. ... Obtain silica sand. Also called quartz sand, silica sand is the primary ingredient in …
حقوق النشر © 2024.Artom كل الحقوق محفوظة.خريطة الموقع