The Comprehensive Guide to Cement Plant Costs: …
TO Download this post and all the books and excel sheets and my personal notes and presentations I collected about cement industry in the last 30 years click the below paypal link ... European Equipment Cost ($) Raw …
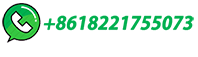