An efficient approach to utilize copper smelting slag: …
The hazardous components of copper slag are released into the ambient environment (Li et al., 2021a, Li et al., 2021b, Zolotova et al., 2021), resulting in …
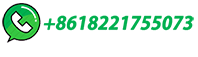
The hazardous components of copper slag are released into the ambient environment (Li et al., 2021a, Li et al., 2021b, Zolotova et al., 2021), resulting in …
Download scientific diagram | Copper slag cover in induction furnace (left), Al-chip melting in rotary furnace with salt slag (right) from publication: Melt Treatment of Copper and Aluminium ...
Large amounts of copper slag are produced every year and major fractions of it are currently disposed, not withstanding the multiple ways the material can be used. …
During the last few decades, the pyrometallurgical processes used for cleaning copper smelting slags have been steadily optimized. The electric furnace or rotary slag-cleaning furnace are now …
The efficiency of the magnesia-activated blast furnace slag for S/S of copper-contaminated soils is evaluated in the present study. The following findings are drawn from the testing: (1) Decrease in the maximum dry density and an increase in the optimum moisture content is observed with increasing percentages of GM. The …
Copper slag is a by-product of copper extraction by smelting. During smelting, impurities become slag which floats on the molten metal. ... Gbfs Blast Furnace Slag. Supplier Of Slag Inquire Now Add to Favorites Jan-22-21 Angelica Dagindob (1.1) …
China's copper resources are characterized by low grade and complex composition. A large amount of copper smelting slag (CSS) containing valuable elements such as copper and iron is produced through smelting. ... Cleaning of a copper matte smelting slag from a water-jacket furnace by direct reduction of heavy metals. J. …
The recovery of copper from reverberatory furnace slag utilizing flotation has been studied. The effective factors such as particle size, pH, the amount and type of collector and additives, and flotation time were examined. The effect of cooling rate on flotation behavior of the slag was also studied. For an air-cooled slag at optimized ...
Fayalite is the main phase of copper slag and a type of Fe silicate glass that is composed of a polymerized network of silicate tetrahedrons, in which SiO 2 and FeO are generally considered as network formers and modifiers, respectively. The structure of fayalite is shown in Fig. 13 [107].In iron silicate glass, O 2− exists in the form of bridging and non …
Immiscible glycerol solution and silicone oil systems in the cold model experiments were used to simulate the matte and slag systems in the copper smelting furnace. In different glycerol-silicone oil systems, air was fed by a syringe pump at different injection flow rates and glass nozzle sizes to control bubble size. The bubble size could be ...
Large amounts of copper slag are produced every year and major fractions of it are currently disposed, not withstanding the multiple ways the material can be used. Application of the slag is often limited by the presence of hazardous elements and their leaching behavior so they can potentially pollute soil, surface water and underground …
Pyro-metallurgical copper slag (CS) waste was used as the source material for ultrasound (US) silica extraction under acidification processes with 26 kHz with HCl, HNO3, and H2SO4 at different ...
The nature of these infiltrations were identified; all the refractory brick samples had been substantially infiltrated by copper and slag elements (mainly copper and iron oxides). The new phases formed were the result of the complex chemical interaction between the slag and the constituent of the refractory.
Copper slag and stainless steel slag of Electric Arc Furnace (EAF) are two typical metallurgical solid wastes, which contain a large number of valuables, such as Fe, Cr, and Cu. The transition metal elements in the waste slags, such as Cr and Fe, can be recycled as the coloring ions in the black ceramic tile. ...
To recover copper from copper slag, a novel slag cleaning method was proposed. The thermodynamics and binary phase diagram of FeO–SiO 2 were …
Ausmelt furnace slag contains about 0.9% Cu (mass %). With increasing the amount of Ausmelt furnace slag, the recovery of copper from it will produce an enormous economic yield. The recovery of copper by floatation from slow cooled Ausmelt furnace slag was studied in...
Copper slag cleaning using the flotation method and/or in an electric furnace is widely adopted in industrial production.[2,3,4,5] The flotation method has the …
Secondary copper blast furnace slag was treated with carbon to derive the conditions for maximum recovery of copper with minimum simultaneous reduction of iron oxide. Experiments were carried out to study the effects of parameters such as temperature, carbon addition and CaO addition to the slag on the efficient recovery of copper. A two …
The morphological structure of the copper slag was characterized by Scanning Electron Microscopy (SEM) (JEOL JSM 7001 F FE-SEM). The observation was performed in a vacuum mode with a 30 kV voltage, the EDS imaging was also conducted for analyzing the element distribution with energy resolution of 15 eV (Li et al., 2023, Liu …
To recover copper from copper slag, a novel slag cleaning method was proposed. The thermodynamics and binary phase diagram of FeO–SiO 2 were calculated first. Then, the effects of experimental parameters on the reduction of Fe 3 O 4, recovery of copper, and slag cleaning mechanism were investigated.The results showed that the …
The maximum recovery of copper in alloy phase was obtained with 5% (by weight) initial carbon in the feed, 2% (by weight) CaO addition to the slag and a …
Slag is further cleaned in a slag cleaning furnace or directed to slag flotation. The SO 2 gas generated during the smelting stage is led to an acid plant to produce sulfuric acid ... Related to the slag copper content, based on the industrial experience and data, the distribution of copper to compounds in the slag phase was …
The hazardous components of copper slag are released into the ambient environment (Li et al., 2021a, Li et al., 2021b, Zolotova et al., 2021), resulting in environmental pollution and unsustainable developmental issues. Copper slag contains 29–45 % Fe, 25–40 % SiO 2, 5–11 % CaO, 3–7 % Al 2 O 3, and other nonferrous
of copper from the slag. Experimental Materials. Industrial copper blast furnace slag was used in this study. Slag sampIes received from the furnace were crushed to less than 3 mm, and 100-g slag sampIes were prepared by means of mechanical splitting. Carbon in the form of graphite powder (-200 mesh, 74 fim) containing greater than 99% fixed
The smelting process can be divided into three stages, namely decomposition of high-valence sulphide, oxidation of sulphide, and matte smelting and slagging reaction (Fig. 1).The efficiency of matte smelting and matte-slag separation, as well as the extent of copper losses to slag are mainly affected by the …
Two slags from steel production in the electric arc furnace (Alcalá de Guadaira, Sevilla, Spain) were used: electric arc furnace slag (EAFS) (3–5 mm particle size) originated in the primary metallurgy or fusion and ladle furnace slag (LFS) (0–2 mm particle size) originated in the secondary metallurgy or refining of the molten bath …
The safe and efficient treatment of copper slag (CS) is an important aspect of the circular economy and green development. In order to reduce the negative environmental impact, CS is used as a precursor to substitute different contents of ground granulated blast furnace slag (GGBS) in the manufacturing of alkali-activated materials (AAM)) in this …
In copper anode furnaces, the installed refractory lining is exposed to chemical attack caused by slag and copper oxide. This results in infiltration of the brick microstructure and corrosion of the bricks' inherent components. Increased temperature level changes the temperature and partial pressure during the furnace operation, as …
Volume stability is a critical challenge for the practical applications of alkali-activated materials. To mitigate the drying shrinkage of alkali-activated blast furnace slag-copper slag (AAS-CS), different contents of polyether-based shrinkage reducing admixture (PSRA) and MgO-based expansion agent (MEA) are used in this study.
Copper slag is a by-product obtained during smelting and refining of copper. Copper smelting slag typically contains about 1 wt.% copper and 40 wt.% iron depending upon the initial ore quality and the furnace type. Main components of copper slag are iron oxide and silica. These exist in copper slag mainly in the form of fayalite (2FeO ·SiO 2).
حقوق النشر © 2024.Artom كل الحقوق محفوظة.خريطة الموقع