11.6 Portland Cement Manufacturing
The heart of the portland cement manufacturing process is the pyroprocessing system. This system transforms the raw mix into clinkers, which are …
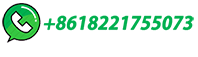
The heart of the portland cement manufacturing process is the pyroprocessing system. This system transforms the raw mix into clinkers, which are …
Hand holding cement clinker nodule on white background, is the basic, raw material used in the production of all types of cement. Save Cement factory, manufacturing has a clinker cooler and accessory equipments.
(57) A process is disclosed for the combined manufacture of steel and cement clinker. Steel scrap is loaded in an electric arc furnace for forming molten steel. Cement paste derived from construction and demolition waste is loaded in the electric arc furnace to act as a flux for the steel to assist in the removal of impurities from the molten ...
The Cement Manufacturing Process. While each cement plant may differ in layout, equipment, and appearance, the general process of manufacturing portland cement is the same: crushed limestone and …
manufacture cement clinker clinker cement Prior art date Application number MA19945A Other languages French (fr) Inventor Jacinto Monge Gutiereez Jose Original Assignee Nac Hulleras Del Norte Sa Empr Priority date (The priority date is an assumption and is not a legal conclusion.
In the cement manufacturing process, the raw mix undergoes a drying process to reduce its moisture content to less than 1%. This dried mixture, known as the raw mix, is then prepared for introduction into the rotary kiln. ... The process of finely grinding clinker leads to a phenomenon known as rapid setting, which occurs as a …
Cement plants have used new grinding equipment, dry-process instead of the wet-process kiln, modern clinker kilns, and multi-stage preheaters that can save energy [1]. The use of blends with renewable fuel and fossil fuel [ 2 ] or the use of solar calcination reactors [ 3 ] can reduce emissions and save energy in cement manufacturing.
Manufacture Process of Cement The manufacture procedures of Portland cement is described below. Mixing of raw material; Burning; Grinding; Storage and packaging; 1. Mixing of raw material ... The size of the clinker is varies from 5-10mm. The lower part i.e. clinkering zone has the temperature around 1500-1700C. In the region lime and clay ...
The cement clinker manufacturing process is a complex process which involves energy conversion and consumption. The objective of this study is to establish the thermal efficiency analytic model of this process. Energy flow models of the whole process and its three process units of raw material preheating & decomposition, clinker …
The clinker manufacturing process. The clinker manufacturing process starts with the extraction of the raw meal from the homogenization silo to insure that the raw meal is stable and homogenized in order to produce consistent clinker quality.
The hot clinker from kiln discharge is cooled very quickly/ quenched in air with the help of efficient coolers. The temperature of clinker is brought to 50oC from 1400oC. ... Discover the detailed steps of the cement manufacturing process in India. Heidelberg Cement offers insights into modern techniques and industry-leading practices.
With this process, we manufactured cement and clinker from industrial and laboratory raw mixes, which had to be rectified by adding kaolinite in compliance with the different cement indicators ...
Cement manufacturing is a complex process that begins with mining and then grinding raw materials that include limestone and clay, to a fine powder, called raw meal, which is then heated to a sintering temperature as high as 1450 °C in a cement kiln. ... including clinker formation. How cement manufacturers can help ensure cement …
Clinker production can be divided into preheating and pre-calcining, clinker sintering, and clinker cooling three stages. Cyclone preheater, cement kiln, and clinker cooler are three main cement manufacturing machines in this process.
@article{osti_6541610, title = {Process of manufacturing Portland cement clinker}, author = {Gottlieb, S}, abstractNote = {Portland cement raw material components are completely calcined before being sintered in a rotary kiln. Clay and limestone are blended to high and low calcium blends, and each blend is fed through separate vertical calciners.
scale, it is clear that bauxite residue can satisfactorily be used in cement clinker manufacture with only slight changes to their operating process. ... Figure 3: Schematic representation of cement manufacturing process 26 Figure 4: Cement production by region 2001 – 2015 34 Opportunities for using bauxite residue in ...
A process for the manufacture of cement clinker and sulphur dioxide from calcium sulphate according to the so-called gypsumsulphuric acid process in which the raw material is preheated in the suspension state by the gases issuing from the kiln. The entrained air issuing upwardly through the seals in the furnace head is used up as tertiary air ...
Order custom essay Cement Clinker Manufacturing Process Manual with free plagiarism report 450+ experts on 30 subjects Starting from 3 hours delivery Get Essay Help. These elements mixed …
Several laboratory and online systems can be employed to ensure process control in each step of the cement manufacturing process, including clinker formation. Cement is a material with adhesive and cohesive properties which make it capable of bonding minerals fragments into a compact whole.
A dry process kiln might be only 70m long and 6m wide but produce a similar quantity of clinker (usually measured in tonnes per day) as a wet process kiln of the same diameter but 200m in length. For the same output, a dry process kiln without a precalciner would be shorter than a wet process kiln but longer than a dry process kiln with a ...
White cement manufacturing process. White cement is a type of special cement, belongs to decoration cement.In general, Portland cement is greyish-green, as the name suggested, white cement is white. In the …
In portland cement manufacturing process, the quality of cement clinker directly affects the quality of the finished product cement. The following are several important factors affecting the cement clinker quality. In the process of clinker production, strict control of these factors can ensure the production of high-quality, high-yield clinker. 1.
The present invention describes a process for manufacture of high iron hydraulic cement clinker using down draft sintering technique, in production of cement and cementation binder for application in construction activity and in metallurgical industry for sintering of iron ore fines and making cold bonded briquettes and pellets. The process is cost effective …
Cement Manufacturing Process . by TIZITA MOGES, SELAMU ABULE & DEREJE ENDALAMAW . ... In cement manufacturing, formation of clinker nodules occurs at the entrance to the hottest part of the kiln with a material temperature of around 1280°C. The clinker is preferably in the form of 10-mm to 25-mm size nodules that exit from the front …
Calcination of raw material. CaCO3 => CaO + CO2. Process emissions of raw material: = 0.54 t CO2/t clinker. Endotherm reaction at 950 °C. ca. 1700 MJ/t clinker ≈ 50% of …
Cement plants have used new grinding equipment, dry-process instead of the wet-process kiln, modern clinker kilns, and multi-stage preheaters that can save energy …
Production Process of Clinker. Cement manufacturers create clinkers through a multi-step process that includes ingredient selection, heating, and grinding. Raw Mineral Preparation – The main …
Limestone plays two major roles in the cement manufacturing process, one is used as a raw material for cement clinker, and the other is used as a cement admixture. Limestone is one of the key raw materials of cement clinker. Around 80-90% of the raw material for the kiln feed is limestone.
Cement plants have used new grinding equipment, dry-process instead of the wet-process kiln, modern clinker kilns, and multi-stage preheaters that can save energy [1]. The use of blends with renewable fuel and fossil fuel [2] or the use of solar calcination reactors [3] can reduce emissions and save energy in cement manufacturing.
Report on Cement manufacturing process - Download as a PDF or view online for free ... The hot clinker is used to preheat the air for burning the coal, and the cooled clinker is stored ready for use. …
حقوق النشر © 2024.Artom كل الحقوق محفوظة.خريطة الموقع