Process of Copper Slag Reduction in an Electric Furnace and …
The main purpose of using an electric furnace in the primary copper industry is the reduction of valuable metals present in the slag after the finished smelting process of …
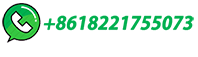
The main purpose of using an electric furnace in the primary copper industry is the reduction of valuable metals present in the slag after the finished smelting process of …
From the World Copper Smelter Survey 2004 it can be estimated that at that time 37% of the smelters used electric furnaces for slag cleaning, 26% used ... (2019) Ugrading copper slag cleaning tailings for re-use. Miner Eng 133:35–42. Article CAS Google Scholar Vadillo A, Mostaghel S, Barati M (2019) Air-blast cross-flow atomization …
The reduction and copper impoverishment of these slags in an electric furnace were simulated in the laboratory as part of a conceptual study for the Las …
Converter copper slag can be viewed as an important secondary resource for valuable metals, considering its high commercial value. The current research investigates the recycling of copper by a combination of theoretical and experimental methods. ... The formation and motion of copper droplets in electric slag cleaning …
In view of the non-renewable reductant resources and carbon neutralization in the process of copper slag cleaning in an electric furnace, this study proposed to use waste …
Copper slag cleaning in an electric furnace consists of two steps: high-temperature reduction, and melt separation through sedimentation. High-temperature reduction, which primarily reduces the excessive Fe 3 O 4 in slag to FeO, is a critical step as it involves a chemical process that depends on many variables. On the contrary, the …
For the context of furnace tapping it is necessary to focus on the liquid products tapped from the furnace. Slag typically consists of an ionic solution of oxides and can be a mixture of liquid ... Development, installation, and operation of a full-copper, deep-cooled slag tap-block for a six-in-line copper slag-cleaning electric furnace. In ...
Copper slag cleaning in an electric furnace is a critical process for reducing the excessive magnetite (Fe3O4) present in the copper slag to decrease the slag viscosity, which can promote the ...
The matte is separated from the slag by difference of specific gravity in the slag cleaning furnace. The matte is further oxidized to form blister copper (Cu: 98.5%) in the converting furnace ...
Download Citation | New process for treating Slag Cleaning Furnace (SCF) flue dust at Atlantic Copper | Atlantic Copper is one of the largest copper producers in Europe. Its production facilities ...
The main function of the furnace is the reduction of the copper level in the slag 11 . Our furnaces are designed for a reduction of the copper level from 1 - 4% down to 0.7 – 0.9%.
The main components of fayalite-based copper slag are iron oxides (FeO and Fe3O4) and SiO2. Based on the slag compositions, the phase equilibrium of this ISASMELT copper slag during the smelting process was analyzed by a FeO-Fe3O4-SiO2 ternary phase diagram (depicted by …
A series of copper slag cleaning experiments with different WCO dosages along with various temperatures and settling durations was systematically carried out in a laboratory-scale electric furnace.
The smelting and converting El Teniente process for copper concentrates as well as slag cleaning furnace technologies to treat slags coming out from the El Teniente furnaces are widely applied ...
Get Copper Slag Cleaning Furnace in Pune, Maharashtra at best price by Ghalsasi Works Private Limited. Also find Furnace Slag price list from verified suppliers with contact number | ID: 4580201448
Molten slag and blister copper collect in the DBF furnace settler and are intermittently tapped via dedicated tap-holes. The slag is reduced in two electric slag-cleaning furnaces operating in series to recover copper in the form of blister and alloy, respectively. The SO2-rich off-gas is de-dusted, dried, and sent to a double-contact double ...
Copper slag cleaning in an electric furnace is a critical process for reducing the excessive magnetite (Fe3O4) present in the copper slag to decrease the slag viscosity, which can promote the ...
Here, however, the slag still contains some percentage of copper and it is treated in a slag concentrator, where rest of the copper is recovered as a slag concentrate and fed back into the smelting furnace. In KCM's Nchanga smelter, the Flash Smelting fur - nace slag is first reduced in a slag-cleaning furnace to a degree, where iron content ...
Mitsubishi process is a technology of continuous smelting of copper sulfide concentrates into blister copper by the smelting furnace, slag-cleaning electric furnace, and converting furnace interconnected by chutes. As the world's first continuous copper smelting technology to realize long-term stable industrial operation, it was researched ...
As shown in analysis step (d) in Figure 2, the rectangular furnace concept is derived based on calculation principles for furnace dimensioning to existing, rectangular copper slag-cleaning ...
copper slag cleaning in an electric furnace could be divided into two steps: reduction and settling. In the reduction stage, excessive magnetite is reduced to provide favorable conditions for the settling. Natural gas, coal, coke, petro-diesel, ferrosilicon, etc., were used
The characterization of two wastes, SWD and CFD, generated in the reprocessed of slag cleaning furnace flue dust from copper smelting have been performed as an essential step towards finding applications or treatments for these wastes. Both waste contain very fine particles size and are mainly enriched of Zn, Pb and Fe. …
Copper loss in the slag of Khatoonabad flash smelting furnace is estimated to be about 1–3 %. At present, the electric slag cleaning furnace is used for the recovery of copper from slag. However, due to low recovery efficiency of electric furnace along with high consumption of electrical energy and water, selection of a method to …
Copper rich oxide slags are melted in electric arc furnace where coke and copper pyrite are added to reduce the copper content in the slag. In order to increase the reaction rate the slag are over heated producing low viscosity aggressive slag.
The system also has additional positive effects during the cleaning and settling process, ensuring that the copper content in the cleaned slag is reduced to a minimum. SMS group offers its customers cooling and lining concepts that increase the lifetime of the furnace significantly. ... Electric slag cleaning furnaces are primarily used in the ...
Outotec Slag Cleaning Slag cleaning at copper and nickel smelters is typically done using an electric furnace process. The design of Outotec slag cleaning furnaces …
The smelting of slag in view producing copper and cobalt alloys achieved at the ''Big Hill Smelter in Lubumbashi'' (DRC) generates Electric Arc Furnace flue dusts as by-product.
It was revealed that although copper losses could be controlled typically at the level of 0.55–1.3 wt.%, depending on the optimisation of the copper smelting …
Copper smelting slag is a solution of molten oxides created during the copper smelting and refining process, and about 1.5 million tons of copper slag are generated annually in Korea. The oxides in copper smelting slag include ferrous (FeO), ferric oxide (Fe 2 O 3), silica (SiO 2 from flux), alumina (AI 2 O 3), calcia (CaO) and magnesia (MgO).
حقوق النشر © 2024.Artom كل الحقوق محفوظة.خريطة الموقع