sbm procedures crushed rock.md · main
sbm procedures crushed rock.md; Find file Blame History Permalink sbm · 34e52685 changjiangsx authored Nov 04, 2022. 34e52685 ...
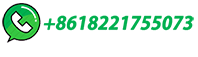
sbm procedures crushed rock.md; Find file Blame History Permalink sbm · 34e52685 changjiangsx authored Nov 04, 2022. 34e52685 ...
• Rock falling • Working in a danger zone PPE or Devices Required: • Eye Protection • Hard Hat • Steel Toe Boots • Snug fitting clothes ... and follow the lock out procedure REPORT ANY HAZARDOUS SITUATIONS TO YOUR SUPERVISOR . 2:35 PM SP-12-02 Page 5 of 10
Follow this simple procedure as advised by Mr. Jean Louis in the program Start Your Own Gold Mine: 1. Find some proper hard surface on which you may crush the rocks which you wish to check for gold. Also obtain a hammer. It is advisable that you use clean, plastic bags, to cover the rocks while crushing in order to protect yourself. Further, eyes …
weak rock may lose strength with time when exposed in cuts. The geotechnical engineer is responsible for choosing design parameters representative of existing and future conditions. Determination of Soil and Rock Properties Subsurface soil or rock properties are generally determined using empirical correlations related to the
1. Primary crushing. As the first stage in a crushing circuit, primary crushing reduces material to a size and shape that can be handled by a secondary crusher. Typically, the minimum setting on most primary …
1.3 The rock correction procedure shall not be used when the percent rock retained on the No. 4 for Method A is less than 10% or greater than 50% (greater than 60% in the case of an aggregate base material); or when the percent rock retained on the 3/4 inch sieve for Alternate Method D is less than 10% or greater than 50%. 2. NECESSARY INFORMATION
Since most of the current researches on the crushed-rock interlayer for highway embankment in permafrost region are based on thermal properties, there are few studies on their mechanical deformation characteristics. In order to study the deformation and failure process of crushed-rock interlayer under the long-term settlement …
Questa Rock Pile Stability Study SOP 8v6 Page 1 Rev. 8v6 10/30/2008 STANDARD OPERATING PROCEDURE NO. 8 SAMPLE PREPARATION (SOLIDS) REVISION LOG Revision Number Description Date 8.0 Original SOP 12/3/03 8.1 Changes VTM, DEW 8.2 Revisions by PJP 5/20/2004 ... • Envelopes for crushed sample .
I'd think closer to 120 pcf - maybe more. For me crushed rock is pretty well-graded and there'd be plenty of finer grains to infill the voids of the larger aggregate. ... 131 pcf depending on just the SG. Also, the void ratio varies depending on the type of rock and procedures used to mine and crush it. So like I said, with all the variables ...
respectively. At both sites, processed rock was fed directly into dump trucks positioned under the crushers' discharge conveyor. Three-axle, rigid-frame trucks hauled the ballast material and 20 000-kg excavators, equipped with clean-up buckets, spread the rock on the subgrade. On average, 27-cm and 30-cm layers of crushed rock were applied ...
Selecting a hard rock, such as river rock or granite, will ensure it lasts a lifetime. Pros of Using Rock in Landscaping. The primary benefit of using rock in landscaping is its cost and labor. Unlike mulch, rock is a one-time purchase and does not need to be consistently refreshed.
Due to the specialized characteristics of the mineral products and the markets for these products, pulverized mineral processing plants have production rates that are less than …
Crushed Stone #10 (Stone dust or screenings): Usually 1/8″ Wide or Smaller. Crushed stone number 10 is the finest grade and is often referred to as dust or rock/gravel screenings. Resembling coarse sand, …
Title: Division 9 Materials - 2025 Standard Specifications for Road, Bridge, and Municipal Construction Created Date: 8/19/2024 9:20:17 AM
PROCEDURES B) If dynamite or cap is observed in rock, do not try to remove it. Shut off crusher and feeder, and call supervisor. 5. A) Equipment starting. 5. A) Turn off, lock out, and tag B) Falling rock from truck or feeder. C) Fall into crusher. D) Struck by slings and hooks, or caught between sling or hook and rock. E) Pry bar slipping.
The standard crushed rock (CR), complying with the standard of road base materials, was obtained from a real construction field. The experiment on CR gradation, compaction and compressive strength ...
Crushed stone often has an angular and jagged edge because of the crushing process. Gravel, on the other hand, typically has a very smooth texture and surface because of the natural weathering and wear of being exposed to running water. …
Gravel size crushed rock is a desirable material for buried pipe support. However, large scale tests to measure strength properties of gravel particles are impractical because of the expense and lack of standard procedures for cohesionless soils. Thus, only presumptive values of the constrained modulus (Ms) for crushed rock are available.
The cost of a crushed rock driveway varies widely depending on several key factors, such as the driveway size, the type of rock selected, depth of the installation, and geographical location. …
Aggregates: Sand, gravel and crushed rock aggregates for construction purposes Author(s) M. R. Smith; M. R. Smith The Institute of Quarrying, Nottingham ...
conveyor belts. The proper procedure is to: 1) Make sure that the belt is carrying a normal load of material that is not segregated; 2) Have the plant operator stop the belt, and use proper lock out procedures; 3) Take a complete cross section of …
Whether you're intending to develop a short stretch of roadway on a smallholding or a network of crushed rock roads covering a huge location, you need to get the essentials right if you want the roadway to last. ... Together with grading, dirt compaction is one of the most important procedures in crushed rock roadway construction. It …
1.1. These methods are intended to apply to coarse aggregates of gravel and crushed stone that have been sized and processed for use in construction items of work. 1.2. This standard may involve hazardous materials, operations and equipment. This standard does not purport to address all of the safety problems associated with its use.
Reclamation test procedures are indicated by "USBR 5123" (for example) and these procedures can be found in the Third Edition of the Earth Manual, Part 2, 1990. iv. I NTRODUCTION Proper pipeline installation involves much more than just covering up …
This report also provides appropriate specification, installation, and commissioning procedures, as well as ongoing inspection and maintenance procedures that can detect non-conformances. ... installed higher touch voltages may be permitted and still present the same risk to personnel as lower voltages with no crushed rock. This …
procedures for crushed rock T13:11:24+00:00 Who we are > Products > Cases > Solutions > Contact Us > Solutions. Copper ore beneficiation plant; Iron Ore Beneficiation Plant; Iron ore powder beneficiation production sand crusher plant; Basalt Crushing Plant in South Africa;
The experimental system for testing the seepage property of crushed rock was designed as shown in Figure 3, which was comprised of four parts: (A) hydraulic pressure system, (B) axial displacement system, (C) ... The experimental procedures are as follows: (1) Crushed ...
The crushed rock ballast shall be fully issued from crushing operations. The crushed rock ballast shall have at least 75 % of the particles by mass with two or more fractured faces and at least 98 % of the particles by mass with one fractured face. The above percentages will be required within each sieve size coarser than ¾ inch (19 mm).
The procedures set forth in this SOP are intended for use with the following SOPs: SOP 1 Data management (including verification and validation) SOP 2 Sample management …
حقوق النشر © 2024.Artom كل الحقوق محفوظة.خريطة الموقع