Sinter Plant Process [8jlkm5rojzn5]
Ironmaking Mathematical Modelling Sinter Plant Process Corus Consulting Limited, Teesside Technology Centre, P.O. Box 11, Grangetown, Middlesbrough, Teesside TS6 6UB U.K. Telephone: +44 (0)1642 467144 Fax: +44 (0)1642 460321 E-mail: [email protected] In order to improve the operation of the sinter plant and the quality of the …
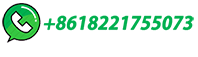