Recovery of Copper and Magnetite from Copper …
Finally, the treated copper slag was crushed and grinded down to 40 μm, and two fractions were obtained by magnetic separation. The magnetic fraction (85%) was mainly comprised of magnetite, while …
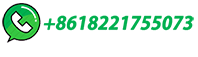
Finally, the treated copper slag was crushed and grinded down to 40 μm, and two fractions were obtained by magnetic separation. The magnetic fraction (85%) was mainly comprised of magnetite, while …
The Waelz slag generated during electric arc furnace dust processing is an iron-rich product with significant amounts of iron, zinc and copper. About 600–800 kg of the Waelz slag is generated per ton of the dust processed. The Waelz slag samples from two different plants were thoroughly characterized using inductively coupled plasma optical …
An innovative technology for direct reduction-magnetic separation with the addition of Na 2 CO 3 and CaO was studied to upgrade copper slag assaying 40.33% Fe total and 0.65% Cu. It is difficult to recover iron and copper from the slag by direct …
The fayalite in copper slag transforms into metallic iron and sodium silicate salt in the activated reduction process, after the following water-leaching and magnetic …
The comprehensive and harmless utilization of copper slag flotation tailing (CSFT) is the key to a waste-free and sustainable copper industry. ... The magnetic separation results indicated that Mo and Cu were enhanced in magnetic products by 34–41 and 15–21%, respectively. Cleaner non-magnetic residues were found to …
In summary, the Fe 3 O 4 and Fe 2 SiO 4 in the copper slag could be reduced to the metallic iron by coal-based direct reduction and recovered by magnetic separation. The best reduction conditions were those in which the reduction temperature was 1300 °C, the reduction time was 30 min, the dosage of coal addition was 35 wt.%, …
In recent years, extensive studies have been carried out to recover the valuable metals from copper slag, involving in magnetic separation (Zheng and Xiao, 2011), selective agglomeration-reverse flotation (Subrata et al., 2015), slag modification-physical separation (Guo et al., 2016), smelting reduction (Prince et al., …
Copper smelting slag (CSS) is a by-product of modern copper production. In this study, iron resources were extracted from copper smelting slag using chlorine roasting and magnetic separation techniques for the first time.
An innovative technology for direct reduction-magnetic separation with the addition of Na 2 CO 3 and CaO was studied to upgrade copper slag assaying 40.33% Fe total and 0.65% Cu. It is difficult to recover iron and copper from the slag by direct reduction since the iron mainly occurs in fayalite and the copper exists in copper …
Quantitative characterization and magnetic separation of copper pyrometallurgical tailing for molybdenum and copper pre-concentration and cleaning of environmentally hazardous elements ... Characterization and recovery of copper from converter copper slag via smelting separation. Metall. Mater. Trans. B, 49 (2018), pp. …
Approximately 2.0–3.0 t of copper slag (CS) containing 35%–45% iron is generated for every ton of copper produced during the pyrometallurgical process from copper concentrate. Therefore, the recovery of iron from CS utilizes a valuable metal and alleviates the environmental stress caused by stockpile. In this paper, a new method has …
Contribute to legaojm/m development by creating an account on GitHub.
By using DR followed by a magnetic separation process for iron recovery from copper slag, Yang obtained iron powder of 92.05% iron content with an iron recovery rate of 81.01%, and Wang obtained iron powder of 92.96% iron content with an iron recovery rate of 93.49%. Both of their tests have achieved good results.
The fayalite in copper slag transforms into metallic iron and sodium silicate salt in the activated reduction process, after the following water-leaching and magnetic separation, about 76% of silicon dissolves into the leaching solution and the metallic iron powders with a recovery rate higher than 90% is obtained.
Copper slag is a solid waste that has to be treated for metals recovery. In order to recover iron from copper slag, the technology of carbothermic reduction and magnetic separation was developed.
Reduction. The reduction process for copper slag is typically followed by magnetic separation [].Depending on the temperature and intensity of reduction, it can …
The experiment of copper-containing slag reduction with hydrogen was carried out. XRD, FT-IR and SEM/EDS were used to examine the effects of temperature and reduction time on phase composition and surface morphology of the slag before and after reduction. The analysis results show that the reduction products of slag are metallic Fe and vitreous …
BCL slag contains both copper and iron which are of interest and subsequently copper as mentioned can be recovered using flotation and iron be recovered using magnetic separation . talks about past work on recovery of iron from copper slag using direct reduction – magnetic separation which yielded iron concentrate of 90.68% …
Similarly, several studies [12,13,14,15] have also shown the potential of magnetic separation for slag recycling. Magnetic separation is a high-efficiency, low-cost, and selective technique that relies on the …
Iron recovery from lead smelting water-quenching slag by "roasting–grinding–magnetic separation" method ... proposed two routes for the selective recovery of lead, copper, nickel, and zinc from lead slag under optimum conditions. The leaching rates of lead, copper, zinc, and nickel were 92%, 60%, 70%, and 66%, …
A novel process to upgrade the copper slag by direct reduction-magnetic separation with the addition of Na2CO3 and CaO. Powder Technol., 347 (2019), pp. 159-169. View PDF View article Google Scholar. ... Characteristics and mechanism of reduction and smelting-separation process of copper slag. J. Iron Steel Res. Int., 22 (2) (2015), …
The suggested methods for metallurgical recycling from the slag mainly include pyrometallurgical processes (e.g. reduction roasting followed by magnetic separation, smelting reduction, and molten oxidation), hydrometallurgical processes (e.g. chemical leaching and bioleaching), and beneficiation processes (e.g. flotation and …
In this study, a new technique was proposed for the economical and environmentally friendly recovery of valuable metals from copper smelting slag while simultaneously upgrading nickel laterite through a co-reduction followed by wet magnetic separation process. Copper slag with a high FeO content can decrease the liquidus …
In the current study, the selective reduction and magnetic separation technique was adopted to recover iron from copper slag. Calcium salts were used as an additive because studies reported that iron in the slag is difficult to reduce via the reduction method and it is mainly present in the form of Fe 2 SiO 4 in slag; that is why in order to …
The significant expansion of the copper resources market has led to a rapid increase in CSS [13], [25].In China alone, the stockpile of CSS has surpassed 300 million tons (Fig. 1 c) and continues to grow annually [44].As an undesirable by-product, only 10% of the annual production is recycled [40].Existing resource utilization strategies for CSS …
In this study, a novel method to recover copper, zinc and iron from copper slag by SO 2 –O 2 roasting-leaching-magnetic separation was proposed. The effect of roasting experiment conditions were roasting temperature of 900 °C, holding time of 120 min, and φ SO2 (The volume fraction of SO 2 in the mixed gas of SO 2 and O 2) of …
In order to recycle iron from copper slag with total iron content(TFe) of 39.96%(mass fraction),a technique with lignite-based direct reduction followed by magnetic separation was presented.After analysis of chemical composition and crystalline phase,according to experimental mechanism,the tests for studying the effects of different parameters on the …
A novel technology, modified roasting in CO–CO2 mixed gas and magnetic separation, was presented to recover iron from copper slag. The effects of various …
The Pb-Zn slag magnetic separation experiment was conducted using a Davis separator, which divided the sample into its magnetic fraction (MF) and non-magnetic fraction (NMF). Both fractions were dried and subjected to chemical analysis via AAS. ... The separation of the copper-containing amorphous phase (spinel) grains from …
Direct reduction refers to the process of reducing iron minerals in copper slag to metallic iron particles below the melting temperature of copper slag [].Using direct reduction–magnetic separation technology to recover iron resources in copper slag has fair recovery effect and short reaction time, which is the development trend of …
حقوق النشر © 2024.Artom كل الحقوق محفوظة.خريطة الموقع